相关市场调研报告《2017-2022年中国电动汽车行业市场发展现状及十三五投资方向分析报告》
作为汽车产业的重要发展方向之一,国内外各大汽车企业从未停止过对轻量化技术的开发和应用。BMWi3作为第一款进入量产的碳纤维车身设计的车辆,成为碳纤维应用于汽车的里程碑项目。但由于目前碳纤维复合材料成本较高,一直没有实现大规模的推广应用。
日前,中国首款铝制车身的新能源车型——奇瑞小蚂蚁(eQ1)的上市带来了全新的汽车轻量化生产思路及理念,再一次引发了业内对电动汽车轻量化技术的高度关注。由于通过超级轻量化技术平台打造的“全铝空间架构+全复合材料外覆盖件”,使整车重量比传统车减少了30%到40%,在当前碳纤维复合材料成本居高不下的情况下,给我国电动汽车轻量化的发展开辟了新的途径。
目前,国内外在轻量化材料、整车设计、制造工艺等方面的研究和应用已取得突破性进展。然而,轻量化技术颠覆了传统汽车的制造工艺,带来整个产业的变革,使行业的发展仍面临一系列新问题,如轻量化评价及测试标准尚未完善、产业间缺乏融合、新型材料成本较高、固有开发模式尚未突破等。因此,亟需企业调整思路,面临行业变革所带来的挑战。
电动汽车轻量化技术取得突破性进展
实现汽车轻量化的主要途径有三种:一是使用轻量化材料;二是优化结构设计;三是采用先进的制造工艺。国内外车企纷纷从这几方面入手,推动电动汽车轻量化发展,并取得了一定成绩。
1.、应用碳纤维复合材料减重显著
高强度钢和铝合金都可以在一定程度上实现车身减重,而汽车用工程塑料和复合材料则对车体的减重最为明显,由此成为汽车轻量化的首选用材。发达国家已将汽车用塑料量的多少作为衡量汽车设计和制造水平的一个重要标志。2015年,我国车用塑料的用量已经达到1046万吨,而且呈逐年上升的趋势。
复合材料具有重量轻、强度高、加工成型方便、弹性优良、耐化学腐蚀和耐候性好等特点。在复合材料中,碳纤维复合材料的应用一直备受瞩目。选用碳纤维增强复合材料制作结构件、覆盖件,可减轻质量达30%左右,对于比燃油车更需要轻量化的新能源汽车,碳纤维增强复合材料有更大的应用潜力,在未来汽车轻量化中将会起到举足轻重的作用。
宝马i3在碳纤维复合材料的应用方面取得了令人瞩目的成绩,是第一款实现量产的采用碳纤维车身设计的车辆,其整备质量仅为1224kg,比设计之初减轻了250-350kg,很大程度上弥补了电池增加的重量。
2、全新制造工艺减少零部件数量
碳纤维的应用将会带来一场革命,其原因在于碳纤维在汽车上的应用改变了传统汽车的设计思想、开发流程及制造工艺。碳纤维材料是可设计的,其零件工艺是多样化的,未来碳纤维应用于汽车没有标准化的材料,整个车和零件的开发过程就是材料开发过程,也是工艺开发过程。
铝型材的三维弯曲、钢铝焊接以及碳纤维零件的成型是目前面临的全新工艺。采用新工艺可大大减少零部件使用数量,实现轻量化目标。其中,碳纤维总成的方式已取得突破性进展。在兰博基尼SestoElemento的项目中,将前围、地板、后围集成为一个整体式座舱,取代了传统结构的48个零件,把零件分为4—6大片,成型之后直接粘接,工艺简单,减重效果突出。整备质量在加注燃料和其它液体之前只有960公斤。
3、结构优化提高材料利用率
汽车车身结构轻量化采用结构优化设计方法,可以在保证车身结构性能要求的前提下,提高材料的利用率,减少冗余的材料,而达到车身结构轻量化的目的,结构优化主要包括尺寸优化、形状优化、形貌优化和拓扑优化。
拓扑优化作为结构优化的一种,不同于车辆构件的尺寸优化和形状优化,是对布局和节点联接关系进行优化,使结构的某种性能指标达到最优化。汽车厂在新车开发时,公司决策层会给出一个整车定义,包括车多大多重,涉及到成本控制,同时希望车达到什么性能。拓扑优化能够在给定设计空间,给定设计重量、设计性能的约束下,迅速得到一个布局和节点联接基本判断,为设计人员提供结构质量最轻、性能最优的力学传递路径方案。
目前,湖南大学已经用拓扑优化的办法对电动汽车的骨架进行优化。基于拓扑优化方法的轻量化策略相比常规轻量化方法可节约30天左右的开发时间、多减重22.4kg,同时还可以不同程度的提升整车性能。拓扑优化的方法已在电动汽车全铝车身的轻量化上已经实现了成功的探索。
湖南大学研制的第二代样车实现了比第一代纯电动汽车整备质量减重18.5%,白车身骨架质量(不包括门盖)由120kg减为90kg,减超过20%,实现了通过车身减重来降低电池成本的目标。此外,湖南大学利用拓扑优化的方法通过五轮迭代,将电池包的结构和整车结构结合在一起,可将电池直接装在车体本身。
电动汽车的轻量化不能仅仅追求材料、制造工艺或结构设计的某一方面,而是需要三者互相结合、互相制约,需要根据实际情况平衡各方面的关系,以便最大程度的实现车辆的轻量化。
如奇瑞新能源汽车eQ1在产品设计上,采用了更加适应电动车的全新的架构设计、平台化的整车及系统设计以及高安全性设计。生产工艺及制造方面将传统的汽车制造四大工艺过程简化为焊接和总装并大量采用了线下分装和模块化供货,缩短了流水线的长度。创造性的提出了全铝骨架车身平台的共享理念。
我国电动汽车轻量化道路仍面临阻碍
我国轻量化技术的发展起步较晚,缺乏经验,与国外先进水平有较大差距,发展电动汽车轻量化仍面临阻碍。
1、轻量化技术标准体系缺失,发展目标尚不明确
目前,我国还没有完整的汽车塑料零部件技术和产品标准,包括技术方面的测试标准以及轻量化技术的完整评价系统尚未完善,需要经过大量的数据积累来形成指导行业的统一标准。
从国际上看,美、日、欧都有轻量化明确的发展指标和路线。以美国整车轻量化的发展目标为例:2020年要在2013年的基础上降重20%,2025年降重30%,该目标还对整个组成系统各部分的减重指标提出了要求,要求整个车身系统减重35%,底盘减重25%,动力总承减重15%。说明该目标非常细致的研究了轻量化实现的路径,对我国汽车轻量化相关标准的制定有一定的借鉴作用。
2、产业融合缺乏,产业链尚未建立
轻量化技术需要运用多学科交叉融合所形成的的综合性、系统性知识,实现跨产业协同,但我国汽车企业与材料企业的融合仍十分缺乏。目前,国外主要车企均与材料企业形成紧密的战略合作关系,跨国公司也已形成“碳纤维复合材料+零部件供应商+主机厂”的产业化布局。
碳纤维和新能源汽车的融合将带来新一轮的革命,如果自主品牌不提早进行布局很可能在这一轮新的革命中被甩开。各跨国汽车集团的材料标准和制品性能标准自成体系,国内供应商实质上很难进入跨国汽车集团的供应链。目前,铝合金、碳纤维等材料供应链在国内也较为稀缺。对于汽车轻量化而言,加快建立起涉及“先进材料研发-原材料生产-零部件制造-整车集成应用-回收再利用”等全产业链的需求迫在眉睫。
3、材料和加工成本高,新型材料应用有限
目前车用轻量化新材料的成本普遍都偏高,国内每吨铝合金的材料成本达4.5万左右,碳纤维的材料成本则每吨高达80万左右,让很多中低端车型在碳纤维的使用上望而却步。此外,材料的加工成本控制难度大,特别是碳纤维复合材料,由于目前国内技术尚未达到一定水平,加工效率低,导致成本进一步增加。对于企业来说,采用新型轻量化材料意味着传统生产设备的改造,四大工艺中冲压、焊接、涂装生产线基本都需要面临着大幅改造或者重建,需要投入大量人力及财力,增加了轻量化材料的推广难度。
4、固有开发思维难突破
汽车轻量化给国内汽车企业带来四大方面的挑战:产品结构创新、新材料应用、新工艺的创新以及整个开发流程的变革。特别是碳纤维的应用改变了传统汽车的设计,开发流程、设计思想以及制造工艺。在实践过程中,大多数企业难以突破固有思维模式,甚至以钣金车体的思维来套用碳纤维的应用。此外,轻量化要求更多的创新思维,例如传统的副车驾有八到十个零件,如果将包边儿的概念用到副车驾上,零件数量则大大减少,焊接越少则强度越高。这不仅是新工艺的问题,而需要通过工艺创新的思维来解决。
5、人才短缺,技术研发能力不足
轻量化技术的发展需要既懂材料又懂汽车的跨学科人才,目前由于缺乏交叉学科人才,材料、工艺、整车厂之间互不了解,厂商与科研团队之间沟通不畅,产、学、研结合程度不紧密,没有合理分工,基础性研究和技术开发研究有机衔接不够,严重阻碍了轻量化进程。
对我国发展电动汽车轻量化的建议
1、建立标准体系
零部件生产技术及产品标准的缺失会导致企业没有明确的研发、生产目标及规范,不利于行业持久健康的发展。目前应尽快建立我国自身的材料认证体系,进行材料的性能检测、应用验证、技术稳定性与安全可靠性评价等。
2、加强各领域结合,尽快建立产业链
轻量化技术的发展应是各相关领域相互协调、相互配合,要鼓励产业链上下游合作,组建产业联盟,支持汽车工业与国内材料行业之间深入交流,实现强强联合,让一部分性能稳定、品质过硬的国产材料优先进入汽车产业链。
3、调整固有模式,广泛利用资源
汽车电动化颠覆了传统内燃机,而轻量化则又颠覆了整个车身,由此带来设计、工艺、装备的变革,原有的技术存量将逐渐被淘汰。企业当前应直面科技革命和产业重构带来的影响,调整生产平台及开发模式,利用广泛的国际资源来实现目标,建立新兴组织结构模式。在新的变革中,原料供应商将变成部件供应商,随之而来的还有回收再利用的问题,以及零部件成本降低带来的整车厂建设投资等一系列的改变。
4、培养跨行业人才,提高创新意识
目前我国汽车轻量化领域跨学科人才缺乏,导致技术研发能力薄弱,应加强跨学科人才的培养,建立“外培项目”,提前储备交叉学科人才。此外,面对产业的变革,研发人员需突破旧有的思维模式和研发思路,提高创新意识,以适应产业变革的需要。
资料来源:公开资料,报告网整理,转载请注明出处(ww)。
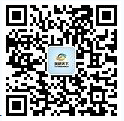
【版权提示】观研报告网倡导尊重与保护知识产权。未经许可,任何人不得复制、转载、或以其他方式使用本网站的内容。如发现本站文章存在版权问题,烦请提供版权疑问、身份证明、版权证明、联系方式等发邮件至kf@chinabaogao.com,我们将及时沟通与处理。