一、前言
金属制品业是机械装备行业的一个子行业,包括结构性金属制品制造、金属工具制造、集装箱及金属包装容器制造、不锈钢及类似日用金属制品制造等,是钢铁、有色等基础金属的重要下游用户。与通用设备、专用设备、铁路设备等机械细分行业一样,金属制品业也是衡量一个国家制造业实力强弱的代表产业。近年来,随着中国经济进入新常态,中国金属制品业也面临着转型升级的挑战。
二、金属制品业转型升级的必要性
加入世贸组织后,我国金属制品业经历了工业化驱动,实现了高速发展,其中线材制品、集装箱、机械零部件、金属容器等重要产品的产量都位居全球第一;整个金属制品业在国民经济中的重要性逐步上升,2015年工业增加值占全部的比重达到3.1%(见图1)。随着国内经济发展进入新常态,金属制品业也面临诸多挑战,直接表现在企业收入放缓和盈利能力下降。
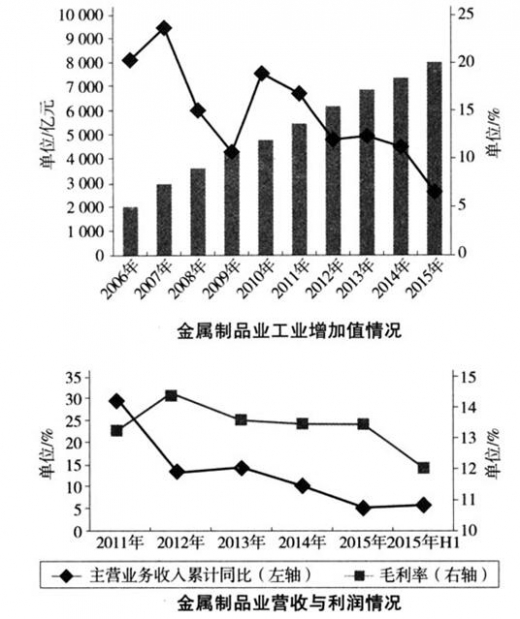
在中国经济高速发展时期,整个制造业可以依赖资源、资本要素的粗放式投入,充分利用人口红利、用工成本低的优势实现发展,但企业产品附加值低、生产效率低——这在包括金属制品在内的机械行业中普遍存在,从投入产出消耗系数看,中间要素投入的比率占比始终较高,2012年达到了81%。另一方面,产品的质量、附加值低,导致产品很难有较高售价,造成行业的增加值率低,只有19%。反观日本同行,以精益制造闻名全球,其产品质量、性能都处于较高水准,同时其制造效率、工艺成本始终控制在较合理的水平,其增加值率基本稳定在46%、中间投入率约54%。因此,中国金属制品行业整体上在增加率、资源要素使用效率上与制造强国有着较大差距。
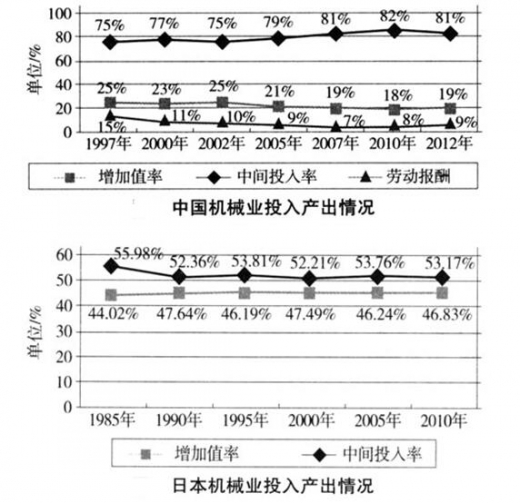
而在低增加值率的条件下,企业同时又面临人工成本劳动报酬的持续上升,企业的营业盈余将面临严重侵蚀,最终走向亏损,同时也造成企业没有足够的资源投向技术创新和转型升级。
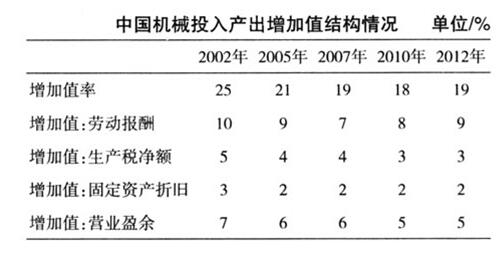
从对比来看,我国金属制品行业在降低中间要素投入、提升增加值率上存在巨大的空间,未来几年内行业转型升级的首要任务是提升产品质量、提高生产效率。这点也与国家供给侧改革、“中国制造2025”战略第一期目标相一致。
与上游采矿、钢铁行业发展进入“低速、亏损”状态不同,2015年金属制品全行业实现利润总额2 102亿元(见图5),同比增长4.7%。整个行业处于一个换挡调整期,这也为行业实施转型升级创造了时间。对于金属制品行业来说,未来要避免陷入和钢铁行业一样的大面积亏损、复苏艰难的窘境,就必须未雨绸缪,着手实施转型升级。
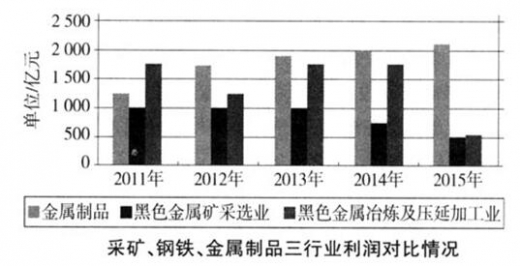
三、行业存在的特殊性
在转型升级的目标上,金属制品业与大部分制造业基本一致,都追求提质增效;但从中国金属制品行业结构特点看,又存在一定的特殊性;行业存在大量中小型企业,2016年上半年纳入国家统计局统计范围的企业有20 525家,而其中在沪深两市上市的金属制品企业仅52家。
下面以上市公司和全行业为对象,做个对比分析。从规模来看,2016年上半年52家上市公司的平均营业收入是19.2亿元,而行业的平均营业收入是1亿元;从员工人数来看,上市公司平均员工人数达到4 052人,而全行业平均员工人数只有167.7人。以这两个指标可以推断:在金属制品行业,大部分企业仍然是营收只有几千万、员工人数只有100多人;整个金属制品行业大部分企业仍然是中小型企业,而且这部分企业数量众多,达上万家。
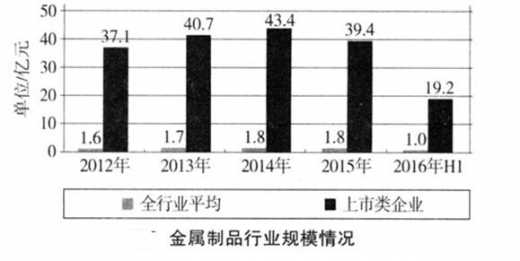
1.劳动密集型特征显著,成本控制要求更迫切
从行业从业人员数量看,截至2016年上半年,全行业从业人数达到343.3万人;而同时,人均工业增加值却只有22.8万元,远低于同类型的通用设备、铁路交通装备的同类制造业的指标。可以说,金属制品业劳动力密集型的特征很显著。
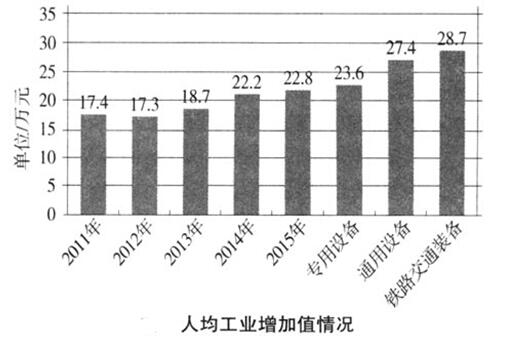
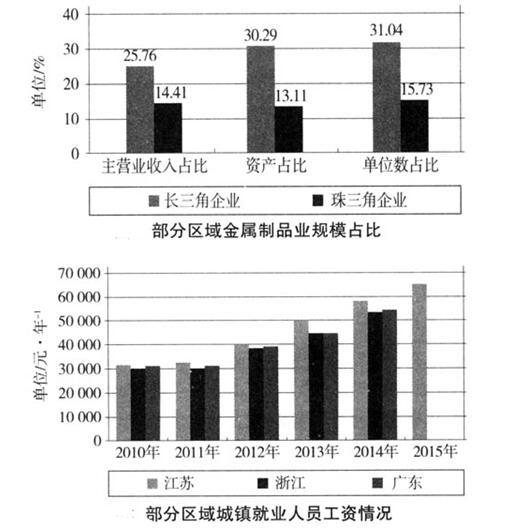
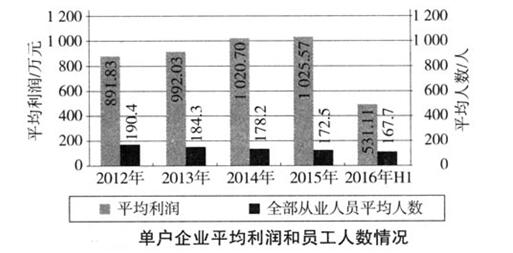
2.对质量管理、生产效率提升需求更多
中小型企业往往在管理上比较粗放,在质量、工艺、标准等方面的内控要求无法与上市公司相提并论,对新工艺和新装备的投入少,最终表现为中小型企业在毛利率和人员效率上均低于大型上市企业;这点从金属制品行业毛利率和行业人均销售收入的对比即可得到印证,两者毛利率相差12%,人均销售收入相差10%。
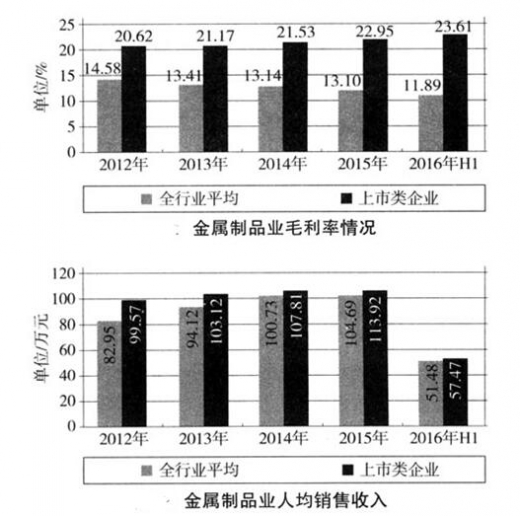
3.安全环保问题更加突出
从行业特点来看,金属制品生产制造过程中往往会涉及到酸洗、热处理、高温、粉尘等危险源,而中小型企业往往缺乏有效的安全、环保管理制度,导致其安全环保问题更加突出;2014年,昆山中荣金属制品公司粉尘爆炸,造成75人死亡的特大事故,凸显了金属制品和中小型企业的安全生产问题,这也对未来金属制品企业转型升级提出了较高的要求。
4.企业资本支出有限,无法进行大规模装备的更新升级
受制于规模因素及融资渠道单一,中小型企业每年不可能有较多的资金投向装备更新、升级。从2012—2016年的对比数据可以看出,中小型企业每年用于固定资产投资的资金不过4 000万左右,根本无法与上市公司每年几亿元的规模相比。
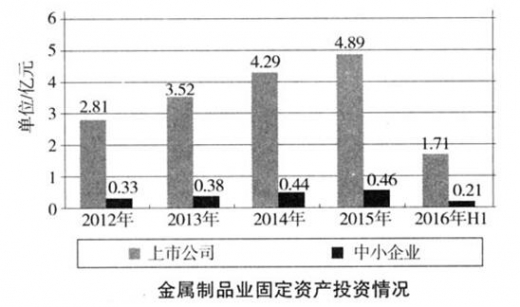
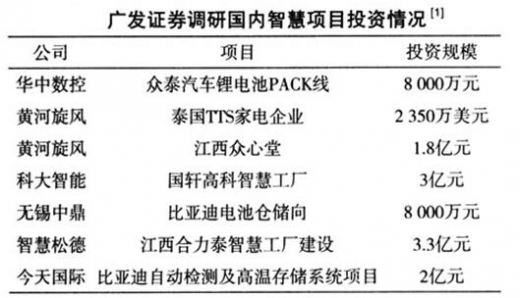
四、金属制品智能装备升级的模式建议
从金属制品转型升级追求的目标和行业存在的特殊性来看,近5年内,金属制品业应该聚焦:提升产品质量可靠性、性能稳定性、环境适应性等指标;提升产品增加值;提高加工生产效率,减轻劳动强度,降低安全风险和企业成本。
相比欧美等制造强国,分析认为国内大部分金属制品制造企业仍然停留在“工业2.0”阶段,“工业3.0”时期的电子、IT、工业机器人等标志性技术仍然没有得到大规模的推广应用;金属制品业并不具备大规模推进“工业4.0”的基础条件;在财务实力上,中小型的企业资本实力,也无法承受“智慧工厂”类的转型升级投资项目。
2015年,国家发布的《中国制造2025》战略中明确提出第一个十年目标:实现国家制造业整体素质大幅提升,创新能力显著增强,全员劳动生产率明显提高,两化(工业化和信息化)融合迈上新台阶,重点制造行业单位工业增加值能耗、物耗及污染物排放达到世界先进水平。具体可采取以下措施帮助金属制品业提质增效:
——提升制造效率方面。发展智能制造装备和产品,组织研发具有深度感知、智慧决策、自动执行功能的高档数控机床、工业机器人、增材制造装备等智能制造装备及智能化生产线,提高精准制造、敏捷制造的能力;到2020年,制造业重点领域智能化水平显著提升,试点示范项目运营成本降低30%,产品生产周期缩短30%。
——提升产品质量方面。提升产品质量,实施工业产品质量提升行动计划,针对包括金属制品在内的重点行业,推广采用先进成型和加工方法、在线检测装置、智能化生产和物流系统及检测设备等,使重点实物产品的性能稳定性、质量可靠性、环境适应性、使用寿命等指标达到国际同类产品先进水平。到2020年,试点示范项目不良品率降低30%。
根据自身客观情况,金属制造业要选择合适的转型升级模式,实现提质增效,唯有借助智能装备,具体可以从以下3方面推进:
——推广生产和装配机器人应用,提升生产效率。工业机器人是由控制单元、驱动单元和执行机构组成的,主要应用于能实现标准化作业的生产线上,比如上料、下料、传输、装配、焊接、表面处理等方面,或用于高温、高噪声、高粉尘、高污染等复杂恶劣的劳动环境下,替代工人完成工作;提高单条产线的加工生产效率,减轻劳动强度,同时也有利于提高加工产品质量,并实现产品加工过程的数据分析和处理。
——推进数控技术与金属制品制造过程的结合,改善产品质量。生产装备的质量决定金属制品的质量,面对现代金属制品业日趋精密的加工要求,具备智能化数字控制能力的机床设备无疑成为金属制品加工行业不可或缺的装备。将工艺参数设定在计算机控制模块,发出控制指令来控制加工装备的伺服、驱动系统或其他执行元件,提升精益制造能力,改善产品质量。
——建立智能化在线质量管理系统。符合人机工程学设计制造,引进在线质量控制技术,实现对金属制品制造过程的气密性检测、间隙检测、油压检测、定载荷试验等检测功能,并将检测数据自动输出给总控系统,实现生产数据统一管理和产品质量可追溯。
总体来说,基于信息处理系统的智能装备等智能技术正在改变着传统的加工方式,数控技术与自动化是提高金属制品业制造水平的关键[2]。通过开发面向中小型企业应用的生产和装配机器人、数控技术、在线质量管理系统,更适合中国金属制品业的客观情况,更能满足提质增效的要求,同时为将来推进智慧工厂提供坚实的基础。
五、总结及建议
从与制造强国的对比来看,近几年国内金属制品业的主要任务是提升产品质量、控制成本、提高生产效率;同时,从行业自身客观情况看,存在大量中小企业,其对控制成本要求更迫切,对质量和效率提升的需求更多,安全问题较为突出,自身资金实力也较弱。这些使得金属制品业的转型升级不能采取“工业4.0”模式,而是要从智能装备入手,推进生产和装配机器人应用、数控技术与制造过程结合,以及在线质量管理系统。
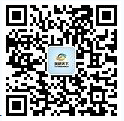
【版权提示】观研报告网倡导尊重与保护知识产权。未经许可,任何人不得复制、转载、或以其他方式使用本网站的内容。如发现本站文章存在版权问题,烦请提供版权疑问、身份证明、版权证明、联系方式等发邮件至kf@chinabaogao.com,我们将及时沟通与处理。