(1)国际铝合金车轮行业现状
铝合金车轮是汽车高速化、节能化和“时装化”的产物,其需求状况与汽车产量和保有量的变动密切相关。
① 全球铝合金车轮发展概况
全球汽车车轮材料主要经历了钢铁材料、合金材料(如铝合金)等演变过程,目前以铝合金车轮为主。从铝合金车轮的发展来看,长时期内,钢制车轮在车轮制造业中占主导地位,但随着汽车工业的飞速发展,人们对车辆安全、环保、节能的要求日趋严格,铝合金车轮以其安全、节能、美观、舒适等特点,逐步取代了钢制车轮。欧洲在20 世纪初就开始使用砂模铸造铝合金汽车车轮,在赛车上得到应用;1958 年有了整体金属模铸造的铝合金车轮,开始运用到普通乘用车;1997 年,欧洲主要汽车制造商以钢轮作为标准配置的比重约为77%,北美平均65%,日本平均60%;到1999 年,英国市场销售的汽车中,钢轮作为标准配置的比重一下降到46%,美国市场则不足40%。目前,世界上铝合金车轮的装车率已达到60%以上,其中乘用车绝大部分选择了铝合金车轮。
2011 年至2014 年,全球铝合金车轮市场产销量持续稳定增长,全球铝合金车轮生产量从2011 年的2.25 亿只增长到2014 年的2.94 亿只,复合增长率为9.33%。下图为2010 年至2014 年全球铝合金车轮需求统计。
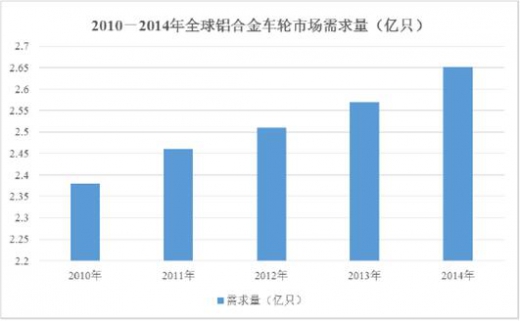
② 全球铝合金车轮产业分布
全球铝合金车轮生产地主要集中在亚洲、欧洲和北美。欧美等国的铝合金车轮生产企业具有较强的工业基础和完善的产业配套,制造技术强,产品质量高,仍然占据着本土高端品牌的市场份额,但由于其本土生产成本偏高,产能已逐步向外扩散,通过在海外(中国、墨西哥、土耳其、东南亚)建厂,降低生产成本,提高竞争优势。
近年来,中国铝合金车轮的产量大幅跃升,从2008 年的5,674 万只增长到2014 年的16,980 万只,增幅达199.26%,约占世界铝合金车轮产量的57.80%。
相比于欧美发达国家,较低的生产成本及巨大的需求市场促使了我国汽车铝车轮行业的高速发展,目前,我国已成为全球汽车铝合金车轮制造中心。
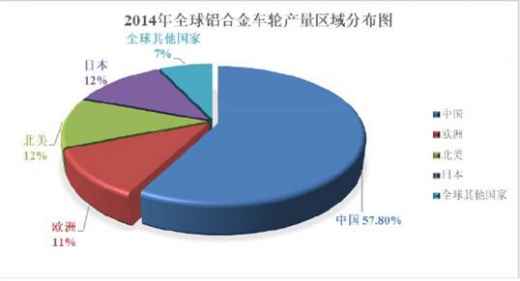
①我国铝合金车轮产量情况
随着发达国家和地区汽车工业产业链向发展中国家和地区转移,优化资源配置,构建全球化采购系统,我国凭借成本优势和产业配套优势,承接包括铝合金车轮在内的关键汽车零部件制造。从1988 年中信戴卡率先开始生产铝合金车轮以来,经过近30 年的快速发展,我国已经成为全球最大的铝合金车轮制造中心。
2008 年至2014 年,国内市场与国际市场对我国所产的铝合金车轮需求量持续稳定增长,年均复合增长率高达20.04%,而同期我国汽车总产量的年均复合增长率只有14.04%。
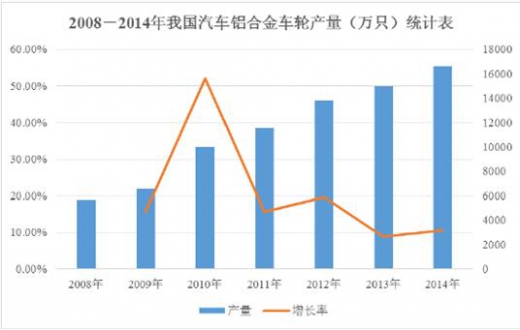
通过持续的技术引进和自主创新,我国少数铝合金车轮制造企业在设计、制造工艺和质量品质方面铸就了世界铝合金车轮行业的领先地位,不仅完全满足中国汽车工业的发展需求,还能批量出口并进入国外知名汽车制造商的全球采购系统。因此,我国铝合金车轮产销量变动除了受国内汽车工业发展情况的影响,还受其他汽车工业发达国家或地区汽车工业发展情况的影响。随着全球汽车产销量和保有量稳定上升以及轻量化、节能化汽车的逐步推广,我国汽车铝合金车轮产业仍将继续稳步增长。
③ 我国铝合金车轮产业的地域分布
铝合金车轮行业,是集资金、劳动力、技术密集于一身的行业,制造技术跨度比较大,工艺控制有一定的难度,产业组织应当实现采购成本、物流成本及人工成本的综合最优化,生产销售区域化,以便于及时供货,加速存货流转,减少流动资金占压。因此铝合金车轮产业逐步呈现出围绕汽车厂家和产业配套的生产销售区域化格局。目前国内铝合金车轮制造厂主要分布在华东地区、华中地区和华北地区等汽车工业发达区域,具体情况如下:
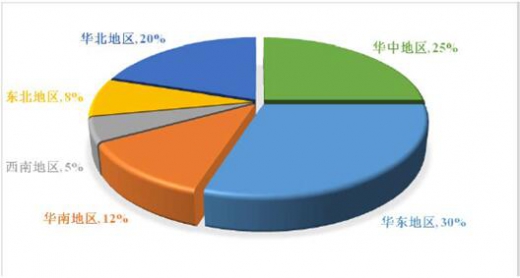
(3)我国汽车铝合金车轮行业特点及发展趋势
①行业生产工艺特点
目前国内的铝合金车轮企业主要采用下列毛坯成型工艺:
A、低压铸造
当前我国铝合金车轮制造业的主流工艺,90%的铝车轮产品采用此工艺进行生产,该工艺生产的产品主要销往OEM 市场(整车配套市场)和海外零售市场。
低压铸造工艺目前在中国大陆已经相当成熟,它的优点是设备造价适中、生产效率高、材料利用率较高、适合少人化生产管理,该工艺已经被所有汽车厂认可。
B、重力铸造
重力铸造工艺是最传统的铸造工艺,目前国内有15%左右的企业还保留有重力铸造生产工艺,产品主要是针对国内和海外零售市场。该工艺的优点是设备造价低、模具便宜;缺点是金属利用率低、生产效率低、性价比低,大部分汽车厂现已不使用该工艺进行生产,在铝车轮制造行业有逐渐被边缘化的趋势。
C、固态锻造
该工艺为比较高端的成型工艺,目前国内只有10%左右的企业采用该工艺进行生产,产品主要供应国内外的大巴、货车及高端轿车市场。优点是产品内在质量好、产品强度高、质量轻;缺点是设备造价高,产品成本高。该工艺生产产品在特定市场具有较大需求。
D、铸造+旋压
“铸造+旋压”工艺分为“低压铸造+旋压”和“重力铸造+旋压”两种方法。
由该复合制造工艺生产的车轮产品具有安全性能好、重量轻、综合性能优越的特点。其中“低压铸造+旋压”工艺逐步被全球汽车厂所接受,呈现出欧美汽车市场及国内SUV 汽车市场的铸旋车轮装车率逐步提升的趋势。
E、液态模锻
液态模锻行业内也被称为半固态锻造,由于该工艺技术难度大,目前国内只有少数企业掌握这种生产工艺。与锻造工艺相比较,其优点是制造工序少、工艺成本低、设备投资少,轮辋可以直接成型。液态模锻产品机械性能接近固态锻造水平,产品性价比高,市场前景广阔。
②行业产品质量特点
铝合金车轮作为汽车整车行驶部分的主要承载件,是左右整车性能最重要的安全部件之一。企业先进的生产、检验设备,完善的质量管理体系和专业技术研发、生产管理团队是保证铝合金车轮产品质量的核心三要素。
铝合金车轮市场分为OEM 市场(整车配套市场)和AM 市场(售后或零售市场)。
OEM 市场中,对于已通过汽车厂复杂、严格的评审认证的铝合金车轮厂商来说,其基本能满足汽车厂对于产品质量和交付期限的要求。但由于不同车轮厂的生产、检验设备,质量管理体系及技术研发、生产管理团队的状况参差不齐,导致不同车轮厂间的产品质量、生产效率和制造成本存在较大差异,汽车厂对不同铝合金车轮OEM 供应商的认可度也有很大的差别。
AM 市场中,市场客户对铝合金车轮厂的生产、检测设备,质量保证体系,技术研发能力,生产管理能力及产品交付能力等方面相较OEM 市场客户对其配套车轮厂的要求来说相对简单。
③行业整体研发能力
对于OEM(整车配套市场)的产品来说,由于车轮的外观造型与整车的设计风格息息相关,所以大部分新车型配套的车轮都是在新车型开发时,由汽车厂委托的设计机构与整车外形同时设计开发出来的,国内大部分车轮厂仅仅参与的是根据样品测绘出产品图并据此转换成模具图。目前,国内只有少数研发设计能力强、质量水平高的大型车轮生产厂才具备与汽车厂进行同步开发的能力,并能够参与到整车产品的同步开发设计中。
对于AM(售后市场)的产品来说,由于生产企业直接面对终端客户需求,所以产品更加注重车轮的外观造型设计。
总之,中国的铝车轮行业已经完全具备现阶段的铝合金车轮产品从外观造型设计,到力学结构测算及加工工艺的整体设计能力。
④行业的发展趋势
汽车消费升级和个性化趋势显现,车轮作为汽车外观的主要组成部分,是外观风格的主要体现。近年来,随着行业制造工艺及技术水平的进一步发展,汽车车轮及市场开始呈现几个大的变化趋势,以彰显汽车的高端、个性化和节能等特点。
高端化:大尺寸车轮日渐主流,车轮主流尺寸从14-15 寸发展到今天的17-18寸。以一汽大众捷达为例,捷达2008 款车型全部配备14 寸车轮,2011 款则有7个版本车型配备16 寸车轮,捷达2014 年款则开始引入17 寸。
个性化:车轮是汽车外观的重要部分,大气个性的车轮为汽车的运动、张扬增添风采。在汽车普及期,车企通常采用多款车车型共用一款车轮是通常的做法,而今天的车企开始为同一款车装配不同风格的车轮,体现其个性化特点。
轻量化:车轮减重是汽车轻量化的主要环节,车轮企业不断使用新的轻量化材料、新的制作工艺来减轻车轮重量,以达到降低车辆油耗的目的。
装备智能化:目前,我国人口红利向下的拐点已经出现,与发达国家相比,曾经的廉价劳动力已然消失,如何提高生产效率、降低人工成本是现存车轮企业和新建车轮企业最为关注的核心问题之一。面对我国制造业“少人化”、“自动化”生产的大趋势,国内铝合金车轮企业为保持自身核心竞争力,未来将对旧生产线进行系统的升级改造,对新生产线进行科学的规划和建设,生产的自动化、智能化将成为我国车轮制造企业的“新常态”。
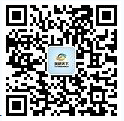
【版权提示】观研报告网倡导尊重与保护知识产权。未经许可,任何人不得复制、转载、或以其他方式使用本网站的内容。如发现本站文章存在版权问题,烦请提供版权疑问、身份证明、版权证明、联系方式等发邮件至kf@chinabaogao.com,我们将及时沟通与处理。