导读:胎圈钢丝技术发展演变情况。随着汽车工业的飞速发展,胎圈钢丝行业也得到了大力发展,特别是大盘重连续化生产工艺在金属制品行业中的应用,有利于提高生产效率,降低作业成本,为胎圈钢丝行业工艺技术发展具有积极的推动作用。
参考《2017-2022年中国胎圈钢丝产业竞争现状及十三五投资策略研究报告》
随着汽车工业的飞速发展,胎圈钢丝行业也得到了大力发展,特别是大盘重连续化生产工艺在金属制品行业中的应用,有利于提高生产效率,降低作业成本,为胎圈钢丝行业工艺技术发展具有积极的推动作用。
胎圈钢丝工艺技术经过几十年的发展,已由原先的冷拉胎圈钢丝发展为回火胎圈钢丝,由镀紫铜发展为镀低锡青铜,钢丝的力学性能和工艺性亦随之得到改善,尤其是粘合力、平直度和残余扭转等指标的量化,使得胎圈钢丝的产品质量明显提高。胎圈钢丝工艺技术的发展演变主要体现在以下三个主要工艺环节:
(1)盘条预处理和粗拉拔的工艺演变
早期的工艺中盘条预处理作业线与拉丝机是分开的,盘条表面处理基本采用间歇式处理,此工艺处理时间长,效率低,还有可能引起钢丝氢脆现象,产品质量存在较大隐患。目前的工艺中,盘条预处理作业线与粗拉丝机连接,实行流水线生产作业,速度快,生产效率高,半成品质量稳定。盘条表面处理工艺有电解酸洗和盐酸处理等,还可采用磷化处理,润滑载体可采用硼砂。
(2)中间热处理和细拉拔的工艺演变
早期的中间热处理工艺主要是指 20 世纪 80 年代,采用马弗炉和电卡炉来完成热处理。热处理后的钢丝强度较低。到 20 世纪 90 年代,该环节工艺有了较大改进,主要采用燃气炉和明火炉进行中间热处理,这两种加热炉控制稳定,劳动强度低,热处理后钢丝强度可提高 100~200MPa。
细拉拔工艺方面,早期采用滑轮式拉丝机,拉拔速度慢,产量低,噪声大,钢丝在拉拔过程中容易扭曲,导致在后道工序很难矫直。目前,细拉拔主要采用直进式拉丝机,实现无扭拉拔,这是消除残余扭转的一个关键环节。在最后卷筒与工字轮收线机的排线器前后各配备一组矫直器,进一步消除钢丝残余应力,并保持平直性。对于胎圈钢丝残余扭转和平直性的要求应在拉拔工序解决 90%。
(3)回火和镀铜工艺的演变
早期回火主要采用明火炉,燃料为重油,这种炉子温度偏差大,炉内气氛不易控制。
如今多采用电加热或燃气回火,这种工艺具有温度点均匀、易控制、钢丝物理性能稳定等优点。回火处理不同于淬火或正火处理,回火处理是深度冷变形钢丝在较高温度下(400~460℃)组织发生回复或局部再结晶,适当调整位错密度,并使部分破碎的晶粒重新集合的过程。回火处理基本保持了冷变形的加工硬化,强度下降 2%~4%,扭转次数降低 15%~20%,塑性显著提高,断裂总伸长率提高到 5%以上,弹性屈服强度提高12%以上。
早期的镀铜工艺通常采用镀紫铜,该工艺下镀铜速度较慢,通常不超过 130 米/分钟。目前胎圈钢丝生产企业多以镀青铜工艺替代了镀紫铜,胎圈钢丝生产企业采用以金属化学置换反应获得钢丝表面镀层的先进工艺,通常称为化镀。为保证镀层与钢丝之间的结合力,提高镀液的稳定性,镀液配方内通常添加稳定剂。化镀工艺具有生产效率高、镀层色泽均匀、与橡胶粘合性能好和防锈能力强等优点。
资料来源:公开资料,中国报告网整理,转载请注明出处(YS)。
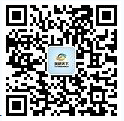
【版权提示】观研报告网倡导尊重与保护知识产权。未经许可,任何人不得复制、转载、或以其他方式使用本网站的内容。如发现本站文章存在版权问题,烦请提供版权疑问、身份证明、版权证明、联系方式等发邮件至kf@chinabaogao.com,我们将及时沟通与处理。