改良西门子法仍是多晶硅料的主流生产路线
现阶段我国多晶硅企业主要采用改良西门子法进行多晶硅料的生产,也有少量企业采用流化床法进行生产。
改良西门子法的生产流程是利用氯气和氢气合成 HCl,将 HCl 和冶金硅粉在一定温度下合成 SiHCl3,分离精馏提纯后的 SiHCl3 进入氢还原炉被在 1100℃氢气还原,通过化学气相沉积反应生产高纯多晶硅。
目前的技术发展方向主要是提高产品质量,降低物耗、能耗、降低多晶硅料的成本。流化床法是以四氯化硅、氢气、氯化氢和工业硅为原料在流化床内(沸腾床)高温高压下生产三氯氢硅、将三氯氢硅再进一步歧化加氢反应生成二氯二氢硅,继而生产硅烷气,制备的硅烷气通入加油小颗粒硅粉的流化床反应炉内进行连续热分解反应,生成粒状多晶硅产品,流化床法生产效率高、电耗低与成本低,适用于大规模太阳能级多晶硅生产。
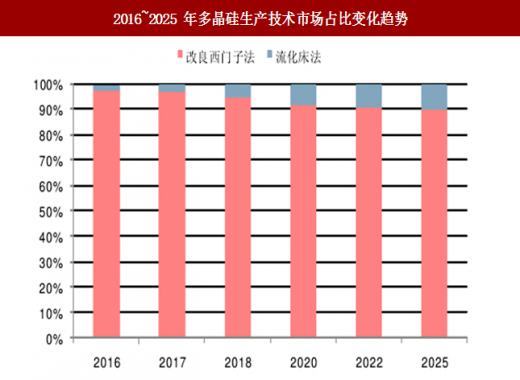
多晶硅生产综合成本将持续降低
根据 2016 中国光伏产业发展路线图,多晶硅环节在还原电耗,冷氢化电耗、综合电耗、水耗、蒸汽耗量、多晶硅综合能耗、硅耗量等方面将随着技术进步逐年下降,余热利用率将持续提升,从而使得多晶硅料的生产成本持续降低。
多晶硅还原是指三氯氢硅和氢气发生还原反应生成高纯硅料的过程,其电耗包括硅芯预热、沉积保温、结束换气等工艺过程中的电力消耗。
目前我国多晶硅还原炉的主流设备为 36 对棒、48 对棒等炉型,还原电耗已降至 52kWh/kg 以下,随着未来大型还原炉的开发和使用、炉内壁材料升级优化、硅管代替硅芯技术、气体配比优化等带动下,到 2025 年还原电耗有望下降至 40kWh/kg 以下。
参考中国报告网发布《2018-2023年中国多晶硅料行业市场规模现状与发展前景评估报告》
多晶硅企业采用冷氢化技术,处理生产产生的副产物四氯化硅,冷氢化电耗包括物料供应,氢化反应系统、冷凝分离系统和精馏系统的电力消耗。当前、行业冷氢化电耗在 9.35kWh/kg-Si 左右、未来通过新反应催化剂的开发、提高工艺环节中热能回收利用率、提高反应效率等,冷氢化电耗仍将稳步下降、到 2018 年有望下降至 8kWh/kg-Si 以下。
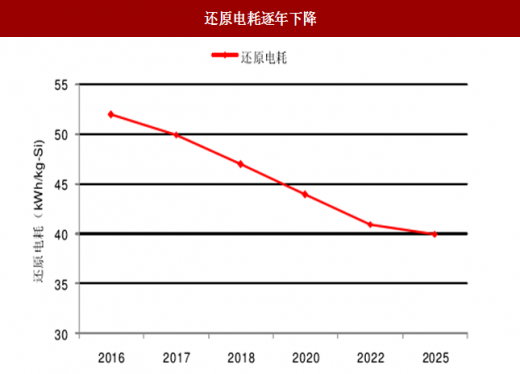
图:还原电耗逐年下降
硅耗量指生产单位高纯硅产品所耗费的硅量(含合成、氢化工序, 外购硅粉、三氯氢硅、四氯化硅等含硅物料全部折成纯硅计算,扣除外售氯硅烷等按含硅比折成纯硅计算,从总量中扣除)。目前, 行业硅耗在 1.2kg/kg-Si。随着氢化水平的提升,副产物回收利用率的增强,预计到 2025 年将降低到 1.08kg/kg-Si 左右。
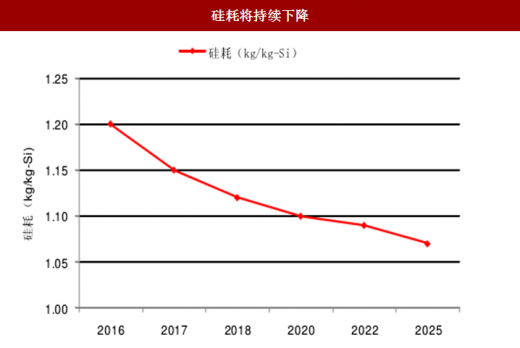

资料来源:中国报告网整理,转载请注明出处(GQ)
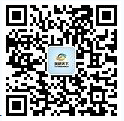
【版权提示】观研报告网倡导尊重与保护知识产权。未经许可,任何人不得复制、转载、或以其他方式使用本网站的内容。如发现本站文章存在版权问题,烦请提供版权疑问、身份证明、版权证明、联系方式等发邮件至kf@chinabaogao.com,我们将及时沟通与处理。