一、三种形态各有优劣,软包电池能量密度突出
目前动力锂电池依据封装形式差异可分为三类形态:圆柱、方形和软包,其中圆柱和方形也统称为硬壳电池。三种动力锂电池的内部构成要素区别不大,核心差异在于圆柱和方形电池主要采用金属材料作为外壳,而软包锂电池采用铝塑膜作为封装外壳。
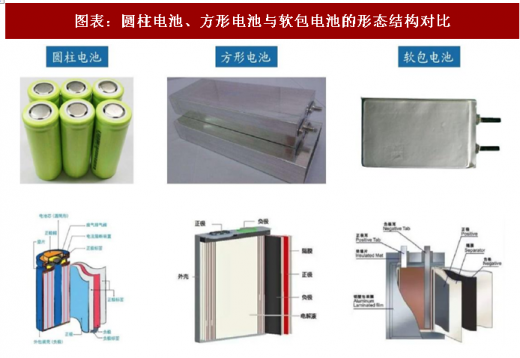
由于特定的包装材料与结构不同,三种电池各在技术性能方面有所差异,各自具备一定的优劣势。
圆柱电池:生产工艺成熟,产品良率高。受益于成熟的工艺,圆柱锂电池PACK成本较低,电池产品良率较高;且散热性能优于方型电池;圆柱形电池可依据具体需求而进行多种形态组合,便于新能源汽车使用空间的充分布局。当下中、日、韩、美等都有成熟的圆柱电池生产企业,比如SANYO、SONY、万向A123等。但是圆柱电池通常是选用金属钢壳或铝壳封装,重量较大,导致电池组比能量相对较低。
方形电池:型号众多,工艺统一难。方形硬壳电池壳体多为铝合金、不锈钢等材料,内部采用卷绕式或叠片式工艺,对电芯的保护作用优于于铝塑膜电池(即软包电池),电芯安全性相对圆柱型电池也有了较大改善。目前,生产方形电池的企业主要有宁德时代、国轩高科、三星SDI、力神等。但是由于方形电池通常是根据产品要求的尺寸定制化生产,造成目前市场上方形电池型号众多,工艺很难统一,对于需要多只串、并联使用的新能源汽车动力锂电池,因此选用标准化生产的圆柱锂电池在生产工艺更有保证,在安全性方面更有优势,同时替换性较强。
软包电池:指以铝塑膜为外壳的锂电池,在3C领域渗透率已经超过60%,并逐步扩展至新能源汽车行业。与硬壳电池相比,软包电池具有设计灵活、重量轻、内阻小、不易爆炸、循环次数多、能量密度高等特点。软包电池随着智能手机和平板电脑的普及得到快速发展,因其良好的延展性和高能量密度特点,逐步应用到新能源汽车、储能等领域。
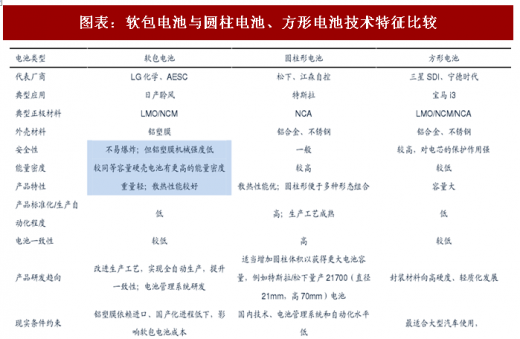
软包装的最大优势在于,能在现有技术水平上提升动力电池的能量密度,在续航里程上进一步缩小和燃油车的差距。根据高工锂电的统计,软包电池比同等容量的铝壳包装电池轻20%,与同样尺寸的铝壳电池,容量高出50%。与硬壳包装相比,软包装能够提升电池安全性、减少电池自耗电、延长使用寿命,并具有设计灵活性。软包装的不足之处在于包装材料铝塑膜机械强度不及硬壳,目前依赖进口、成本较高。
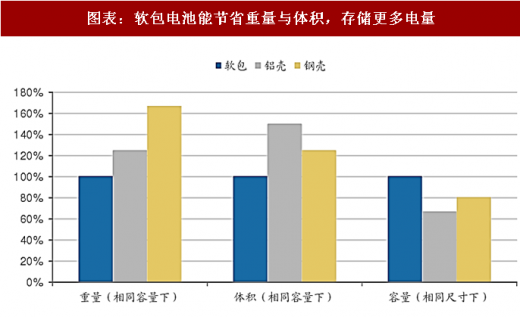
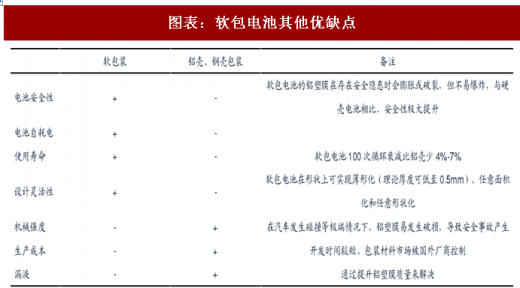
参考观研天下发布《2018年中国动力电池行业分析报告-市场运营态势与发展前景研究》
成本和一致性问题成软包电池发展限制因素。软包电池不足之处在于,目前生产工艺尚不成熟、标准化程度较低、电池一致性较差。不过这些劣势未来通过生产规模化、自动化、增强电池管理系统、铝塑膜质量提升来消除。此外,软包原材料铝塑膜仍有赖进口,动力电池制造厂商对国产铝塑膜接受程度低,这也在一定程度上限制了软包电池的大规模发展。未来随国内企业在铝塑膜领域的产能发力,后续限制性因素有望陆续化解。
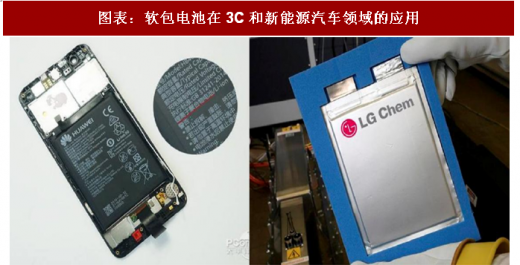
二、未来固态电池适合搭配软包封装技术
按照电解液物质状态的不同,软包电池可分为软包液态电池和软包聚合物电池,前者使用液态电解液,后者使用的电解液目前以胶体为主。以固态物质为电解液的全固态电池仍处于研发示范阶段,将进一步提升动力电池的能量密度和安全性,由于不使用液态电解液,电池封装可使用软包。软包液态电池广泛应用于国产手机、充电宝,著名畅销车型日产聆风即装载了AESC提供的层叠式软包液态电池;软包聚合物电池则用于笔记本电脑及品牌手机。

远期来看,全固态电池能量密度高、安全性最强,有望带动软包装进一步发展。全固态电池以聚合物、氧化物或硫化物等固态电解质代替隔膜和电解液从根本上解决电池安全问题;电池单体能量密度有望提升至400-500Wh/kg。全固态电池目前仍处于研发阶段,宝马、丰田、博世及部分国内企业都在积极布局,未来有望成为主流电池路线。德国Kolibri为奥迪开发出一款大容量的聚合物固态锂电池,电池总重300kg续驶里程达600公里。由于无需使用液体,固态电池外壳与组装工艺得到简化,适宜固态电池封装使用的软包技术有望为软包电池发展打开新的成长空间。
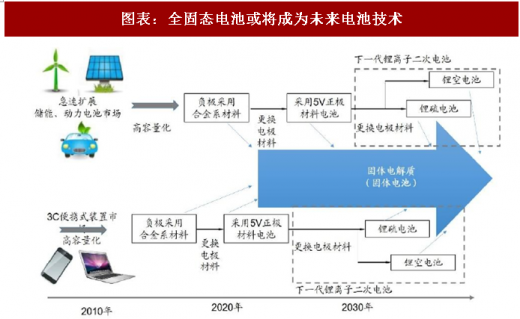
我们认为,短期内软包装作为一种电池轻量化高能化的手段,将以较高比例占据增量市场,长期看好全固态电池采用软包装趋势。新能源汽车新政策释放了推动电池性能提升、增大能量密度的信号。随着补贴门槛的不断提升,软包装能够助力更多电池企业提升能量密度,提升产品竞争力,软包装将在增量市场中占据一席之地。
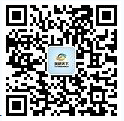
【版权提示】观研报告网倡导尊重与保护知识产权。未经许可,任何人不得复制、转载、或以其他方式使用本网站的内容。如发现本站文章存在版权问题,烦请提供版权疑问、身份证明、版权证明、联系方式等发邮件至kf@chinabaogao.com,我们将及时沟通与处理。