中国报告网讯:
中国GPS导航市场运营分析及竞争战略研究报告(2012-2016)
中国汽车维修市场运营格局及投资方向研究报告(2012-2016)
文章导读:普通板模具一般调试2~3个轮次就可达到品质标准。而高强板模具至少要4~5轮次,有的甚至更高。同样高强板模具在国外也是难点,最近我们承接了一些美国通用的模具,其中就有高强板。在工艺方案上美方也是几易其稿,反复修改方案,并且一再强调没有十足的把握,其中最大的困难就是无法判断回弹。
当前,汽车制造业面临着激烈的市场竞争,尤其是随着美国经济衰退、欧债危机,各大汽车厂商都将眼光瞄准了中国市场,为此汽车制造厂家不断地将最新的车型同步推向中国市场,奔驰、宝马的占有率不断提高,而大众的2011年全球盈利,中国市场占了20%以上,奥迪全年销量的增长中国贡献了50%以上,仅2012年2月份的统计,奥迪系列在中国就卖了3万多辆,创下历史新高。为了提高其竞争力,汽车新车型的开发周期不断缩短,已经从过去的1.5年缩短至1年,并且还将继续缩短。
1.模具三维设计
模具的三维设计是数字化模具技术的重要内容,是实现模具设计、制造和检验一体化的基础。它的优点是:①将模面设计与结构设计分开,前者采用曲面设计,后者采用实体设计;②取消了传统的二维图样,根据各工序的需要给出三维简图和标注必要尺寸的平面简图;③模块化设计,通过模具结构标准化和建立三维标准件库和典型结构库,大大缩短了模具设计时间。一些汽车模具厂家还对拉延模等一些结构典型、标准化程度较高的模具,开发了专用的三维设计模块,进一步提高了设计效率。此外,除了有利于实现集成化制造外,另一个优点就是便于干涉检查,可进行运动干涉分析,解决了二维设计中的一个难题。模具三维设计可以使铸__件泡沫实型完全采用数控加工,从而提高了铸件的精度,为后续的精细加工创造了条件。由于三维设计的结果是模具的三维模型,所以模具的构造面,例如导向面、镶块安装面和螺钉孔等,都可以实现数控加工的编程,有利于提高加工的自动化程度。目前,大部分国内厂家均采用三维设计。
2.模具加工自动化
先进的加工技术与装备是提高生产率、保证产品质量的基础。国外许多汽车模具企业中都配有双工作台的数控机床,自动换刀、工件在线测量系统等已不鲜见。数控加工已由单纯的型面加工发展到型面和结构面的全面加工,由中低速加工发展到高速加工,加工自动化技术发展十分迅速。
目前,在模具生产中已经应用的加工自动化方式大体上可分为三种,即由多台可互换工作台数控机床组成的生产线、柔性加工生产线和一体化加工中心。第一种生产线包括了底面加工、粗铣和精铣等多台机床,工件换机床时不必重新装夹找正。由于机床为多工作台式,工件不需要被重新装夹,因而加工效率很高。一体化加工中心是一种粗精加工一体化的五面加工中心,其优点是除底面加工之外,一次装夹可实现全部加工面的高速、高精度加工,生产效率非常高;缺点是,由于粗精加工在一台机床上完成,长期加工容易影响机床的精度。目前,国内大部分模具厂采用的是机群式加工,即划分机床种类,哪些用于粗加工,哪些用于半精加工,哪些用于精加工。与柔性加工线比,无论是在效率上还是模具质量上都有不少的差距,未来国内模具厂的发展方向应当是柔性加工生产线。
3.高强度钢板冲压技术
高强度钢由于在屈强比、应变硬化特性、应变分布能力和碰撞吸能等方面具有优良的特性,在汽车上的使用量不断增加,其目的就是在汽车发生碰撞时最大限度地保护乘客的安全,最大限度地降低车身的质量。现在,有些车型梁类件已采用抗拉强度高达980MPa的钢板。由于高强度钢板在塑性变形时弹性变形比例较大,因此高强度钢板制件在成形后的回弹和扭曲比普通钢板严重。
目前,AutoForm等CAE分析软件很难对高强度钢板在冲压成形中造的回弹和扭曲变形进行预判,通过计算机模拟的结果往往与实际结果差别很大,严重地影响冲压件的形状尺寸精度。对于高强板零件,其综合合格率能够达到85%以上就相当不错了。目前国内厂家对高强板模具都非常头痛,以比亚迪为例,制造高强板模具的周期远远高于普通板模具,普通板模具一般调试2~3个轮次就可达到品质标准。而高强板模具至少要4~5轮次,有的甚至更高。同样高强板模具在国外也是难点,最近我们承接了一些美国通用的模具,其中就有高强板。在工艺方案上美方也是几易其稿,反复修改方案,并且一再强调没有十足的把握,其中最大的困难就是无法判断回弹。由于我们做过不少比亚迪自身的高强板模具,深知控制回弹的难度,很多时候它的回弹都与你预料的恰恰相反。但是,并不是所有企业都做不好,由于与奔驰合作的缘故,我们了解到,奔驰车上高强度板的应用超过了50%,而且制件合格率很高。当你向他们请教时,他们遮遮掩掩,总是说干得多了,经验丰富了就会好的。所以,我们没有捷径可走,只能靠自己。因此,可以说回弹控制是当前高强度钢板冲压技术最重要的研究方向。这其中包括两个方面,一是进一步提高回弹分析的精度,二是研究合理的模具设计参数,如拉延筋、工艺补充面和压边力等。后者需要我们在大量的应用实践中不断总结和积累经验。
4.级进模、多工位模具和自动化模具的广泛应用
随着汽车冲压生产高效化和自动化的发展,级进模、多工位模具和自动化模具在汽车冲压件的生产中应用将更加广泛。形状复杂的冲压件,特别是一些按传统工艺需要多副冲模分序冲制的中小型复杂冲压件,越来越多地采用级进模成形。在大众、通用、福特和丰田等公司,约有30%~40%的汽车冲压件已采用级进模生产。这类模具是一种高新技术模具产品,技术难度大,制造精度要求高,生产周期长。其技术难点在于排样设计优化、模具结构设计和高精度的制造技术。在这方面,国外公司具有较高水平,他们生产级进模,其模具寿命可高达数百万次。因为级进模的技术含量高,所以其附加值高、模具价格高。与国外相比,我国的汽车冲压件生产用级进模具,在工艺排布、制造精度、结构功能和使用寿命等方面仍存在较大差距,每年还需大量进口。例如整体侧围、翼子板和车门等容易在生产中划伤制件的模具,在国外无疑都是采用自动化模具。即使自主品牌模具现在也开始采用自动化模具,这是未来模具的发展趋势,而我们在这个方面刚刚起步不久,刚刚过渡到从单纯加工自动化模具,到设计、制造多工位级进模具,因此,采用多工位级进模将是我国重点发展的模具产品。
5.模具材料与表面处理
模具材料的质量和性能是影响模具质量、寿命和成本的重要因素。近年来,除了不断有多种高韧性和高耐磨性冷作模具钢、火焰淬火冷作模具钢和粉末冶金冷作模具钢推出外,国外在大中型冲压模具上选用铸铁材料,是一个值得关注的发展趋势。球墨铸铁具有良好的强韧性和耐磨性,其焊接性能、可加工性和表面淬火性能也都较好,而且成本比合金铸铁低,因此在汽车冲压模具中应用较多。
在德国,小型和小批量生产用模具,常选用G G25和铸钢G S45制造;大型和大批量生产用模具,多选用球墨铸铁GGG60、GGG70和含Ni、Mo元素的GGG70L制造。在日本丰田公司,采用基体与刃口一体化的特殊铸铁材料来制作修边模,使模具的制造成本大大降低。铸铁整体刃口经表面淬火处理后,用于薄板料修边模寿命可达几十万次。新型汽车冲模材料的研究与应用,是影响汽车模具发展的一个重要问题。由于汽车模具的尺寸大、用材多,降低模具材料成本对于增强模具产品的市场竞争力具有重要意义。
目前,国内汽车模具的表面处理大多是采用火焰淬火。但是,这种方式有很大的缺点。例如:工件变形、淬火不均匀以及速度慢等。近年来,激光表面强化技术发展迅速,并已成功地应用于汽车冲压模具。激光表面强化技术在模具上的应用主要包括两个方面,即激光表面淬火和激光熔覆。激光表面强化技术,可对不同材料的模具工作表面进行强化处理,以提高模具的使用寿命,修复磨损面。对于采用合金铸铁制造的覆盖件模具,火焰淬火的硬度一般为H R C40~50,激光淬火的模具表面硬度则可达H R C55~65,硬化层的有效深度为0.5mm~0.7mm。激光淬火层硬度均匀,与基体有很强的结合力。由于激光加热速度快,热影响区小,所以被处理的模具变形很小。激光淬火具有较高的处理速度,通常可达0.5m2/h。激光熔覆技术可对模具表面局部损伤部位进行修复,覆层可与模具零件基体形成最佳的冶金结合,修复效果明显优于其他焊接方法。目前,国内许多厂家开始尝试这种技术,这也是模具行业的发展趋势之一。
6.管理的科学化与信息化
模具行业是个特殊行业,类似于流水化生产,又不同于流水化生产。同样的模具,除非复制,否则不可能制造两套完全一样的模具。因此严格意义上说,它是纯粹的单件生产。按说,都是模具企业,管理方式、核算方法应该相似,但是,目前的状况是模具企业各有各的管理方法,而且无论采取何种管理模式,大家都遇到相同的问题。例如:生产计划与交期的矛盾、质量与成本的矛盾,以及如何最大限度提升数控机床效率的问题、成本如何计算才更加合理的问题等。随着E R P的应用,大家都把希望寄托在E R P上。但是,由于模具行业本身的特殊性,没有现成的软件可以应用,只能合作或自己开发,目前一汽与软件公司合作开发了E M A N管理系统,二汽与华中科大开发了自己的管理系统,山大华天与福田模具开发了自己的管理系统,天汽和比亚迪都是自己开发的系统。但是这些系统,都只能应用于自己的企业,别人无法用。而这些软件系统目前或多或少都遇到了开发瓶颈,都有自身无法解决的问题。
管理科学化、信息化这个思路是正确的,依靠管理系统、依靠高科技绝对是正确的,只不过现在的路数可能还不对,就像软件编程那样,还没有找到思路,不过没关系,只要按照管理科学化、信息化这个思路走下去,我们一定会成功。管理科学化、信息化是模具企业的必经之路。
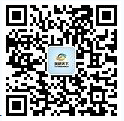
【版权提示】观研报告网倡导尊重与保护知识产权。未经许可,任何人不得复制、转载、或以其他方式使用本网站的内容。如发现本站文章存在版权问题,烦请提供版权疑问、身份证明、版权证明、联系方式等发邮件至kf@chinabaogao.com,我们将及时沟通与处理。