航空产品的大尺寸、复杂外形使得示教编程工作量和耗时过长,单件小批的生产模式又使得喷涂对象经常发生变化,因此方便、快捷的编程方法和可以对喷涂过程进行预览的仿真环境变得十分重要。借助离线编程系统(Offline Programming System,OPS)生成喷枪轨迹是减少机器人生产准备时间的重要手段。
机器人喷涂离线编程与仿真系统的框架如图3所示,其输入是喷涂对象的三维模型、工艺需求和喷涂对象与机器人的位置关系,规划器计算喷涂轨迹后由解释器在仿真环境下进行验证,即通过逆运动学计算机器人的实际运动,确保喷涂过程安全、可实现,然后将轨迹编译为机器人控制程序发送给控制器控制机器人进行实际喷涂。如果采用了移动变位机构,机器人工作空间分析、喷涂区域划分、机器人移动机构的运动等问题都是离线编程系统需要解决的问题。
对象定位是由于飞机的大尺寸和大重量特性难以精确停靠,每次作业前对飞机停靠位置和姿态进行测量,以便将飞机的位置和姿态参数传送给离线编程系统,对喷涂轨迹加以修正。航空业常见的大尺度测量仪器有激光跟踪仪、iGPS等,但目前较先进的整机喷涂系统都集成了自身的定位装置,以降低系统对外部测量仪器的依赖,并减少测量过程中人为干预,提高定位自动化程度,缩短生产准备时间。集成定位系统设计取决于测量技术的选择,如接触式测量装置、激光测距技术和CCD相机等,每种测量技术都有自身的优势和局限。如视觉传感器成本最低,但其自身需要标定,且成像效果易受光线条件影响,对算法要求比较高。
将测量传感器集成在机器人末端,利用一个传感器测量多个标志点,从而减少测量传感器的数量是降低系统成本的有效方式,其本质是将机械臂当做测量臂,利用机器人运动学计算求得测量标识点的位置。
5 工艺方法与装备
目前,溶剂型涂料常用的喷涂方法包括空气喷涂、无气喷涂、混气喷涂、静电喷涂等。其中空气喷涂设备简单,易于操作,效率高,适应性强,是最为广泛的喷涂方式。空气喷涂设备主要分为3大部分:供气设备、供料设备和喷枪。供气设备提供所需要的高压雾化气源、扇形控制气源、枪针控制气源等;供料设备则提供涂料搅拌、涂料输送和控制等功能;喷枪安装在机器人末端,是涂料的雾化和涂敷的主要执行机构。
工艺装备上,空气喷涂存在较大涂料损耗,随着人们环保意识的增强,对减少污染、降低能耗日益重视,高上漆率和低能耗的工艺设备一直都是喷涂技术进步的重要标志。从工艺方法上,保障涂层表面质量、附着力、厚度均匀性,以及减少过喷、避免浪费都是工艺研究的重要内容。
未来新趋势
参考观研天下发布《2017-2022年中国喷涂行业市场发展机遇及投资战略研究报告》
回顾整机喷涂系统的发展历程可以看出,整机喷涂技术在过去的十余年间取得了巨大的进展,但技术的进步是无止境的,现有喷涂系统在喷涂效能、操作性、安全性、可拓展性、设备柔性上还有进步空间。未来整机喷涂系统需要重点发展的关键使能技术包括:
1 更灵活安全的机械臂
由于飞机结构的特殊性,常见的6自由度工业机器人有时无法满足喷涂作业的需求,这意味着未来对专用、特种、非标喷涂机器人的需求会越来越强烈,因为只有针对具体对象和工艺需求进行深入的分析才能引领本体结构的创新设计。例如,冗余自由度设计可以使机器人具有更大的工作空间、灵活性更高,而具有关节力反馈能力的柔性机械臂在发生意外碰撞时更为安全。
2 更智能的编程系统
离线编程相对于示教来说已经极大地减少了程序调试环节的耗时和工作量,但现有的离线编程系统仍需要大量的人机操作,特别是喷涂路径优化、运动仿真、程序检查、程序修正等环节,因此在对工艺深入了解的基础上,将路径规划、机器人轨迹优化、干涉校验、工艺参数与过程优化等环节封装起来,并自动实现,将客户端的操作和对人员的要求降到最低,是未来的发展方向。
3 对象定位与调姿机构
从现有整机系统使用经验看,使用定位调姿装置可减少飞机的定位误差,有利于缩短生产准备时间。但现有工装大多是针对具体对象专门设计的,若能在设计时充分考虑可重构性和柔性,使之适应不同尺寸和类型的产品,并形成软硬件相结合的移动工装,融合搬运、支撑、定位、调姿多功能于一体,不但可大大提高生产效率,且可降低工装的总体开销。
4 新工艺方法和装备
为了获得良好的喷涂质量,需要事先进行大量、反复的试验和调试,这一过程不但耗费大量的时间,而且过分依赖操作者的实践经验,因此深入开展机器人喷涂工艺方法研究,开发集成化工艺过程优化软件,支撑喷涂工艺参数和轨迹优化,对于保证喷涂作业质量稳定性、提高喷涂作业的标准化和规范化程度具有非常重要的指导意义。在喷涂装备上,现有喷涂装置在涂料混合、多种涂料切换以及上料、清洗、保障、监测等环节的自动化和规范化程度上还有提高空间。此外,飞机上存在很多大曲率甚至曲率突变曲面,保障这些区域的涂覆均匀性和上漆率也依赖于工艺方法和装备的进步。
5 多功能末端执行器
从工艺流程上看,涂装作业可以大致分为前处理、喷涂和后处理3个主要过程,包括打磨、清理、保护、喷涂、干燥、测厚、修补等主要环节,喷涂在整个涂装过程中所占的工作量和耗时比例在10%左右,因此喷涂机器人研究不能局限于喷涂本身,将机器人技术拓展应用到整个涂装过程的其他环节,才能有效缩短整个涂装环节的时间,提高作业效率。从现有技术和设备的发展水平看,打磨、清理、测厚、修补等环节都可以探讨机器人化的可能性。
为了支撑这些过程,开发集成或能够快速更换测头、磨具、吸尘装置、清洗装置、测量装置、相机等元器件的多功能末端执行器有助于深化机器人在涂装作业中的应用。
结束语
尽管业内都意识到了机器人整机喷涂的价值和意义,也都积极地进行了各种尝试和开发,但由于系统集成度和复杂度比较高,设备投资比较大,造成系统技术门槛比较高,属于高端制造装备,有需求并掌握该项技术的企业仍属于极少数,技术发展成熟度也没有达到标准工业机器人的水平,没有孕育出成熟的制造商和统一的行内标准。但需求是最强劲的牵引力,我们有理由相信在我国航空制造业高度发展的时代背景下,整机喷涂技术和设备将会取得快速进步,在世界航空制造领域拥有自己的一席之地,这也符合发展具有我国特色的高端机器人技术和装备的大路线。
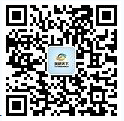
【版权提示】观研报告网倡导尊重与保护知识产权。未经许可,任何人不得复制、转载、或以其他方式使用本网站的内容。如发现本站文章存在版权问题,烦请提供版权疑问、身份证明、版权证明、联系方式等发邮件至kf@chinabaogao.com,我们将及时沟通与处理。