尽管机器人在 3C 领域的发展空间广阔,但 3C 领域机器人的应用是难度最大的。3C 产品生命周期短,工艺繁杂,精密度高,订单量小,客户数量大以及没有国外经验可以借鉴等多种原因阻碍国内 3C 制造自动化的发展。
1. 3C 产品生命周期短工艺更新频繁,“机器换人”面临成本不降反增风险
3C 产品生命周期短,工艺日新月异。其中最典型的同时也拥有最大市场的是智能手机。据调查统计,大众习惯的智能手机更换周期约 2 年,苹果公司所有产品平均更新时间略超 1年。
iphone 作为智能手机的标杆,从 2007 年第一代至今,背板的主材的更替从 2G 的金属,到 3G、3GS 的塑料,到 4G、4S 玻璃,再到 5、5S、6、6S、7、7 Plus 换回金属,再到 iphone 8 传闻中的换回玻璃。
外壳的工艺则从圆边平面背板,到弧面背板,到平边平面背板,再回到圆边平面背板,再到 iphone 8 传闻中的双曲面玻璃。
近十年间,大多数国产智能手机都多少模仿着 iphone 的外形不断更新,仅背板工艺的变换已十分频繁,智能手机内部工艺的升级更是复杂。
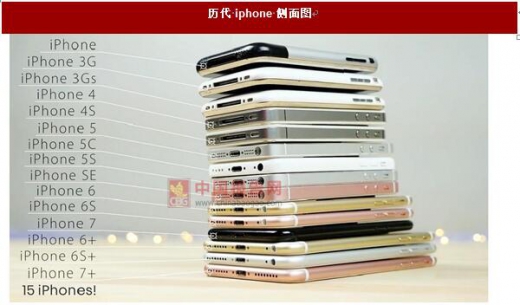
工艺的频繁变化带来机器人功能和性能频繁升级的需求。一旦 3C 产品工艺发生变革性的改变,比如 OLED 屏替代 LCD 屏,机器人原有的精度将不适用于新的生产,曲面屏的使用会使原有的贴合工艺不再适用等等。
在国内,特别是在应用尚不成熟的 3C 领域,制造商出于稳定性考虑往往更信任进口机器人,使用较多的爱普生、雅马哈等 SCARA 机器人价格较昂贵,约 4-5 年的回本期使 3C 厂商面临成本无法收回的大风险,成为阻碍 3C 机器人市场发展的原因之一。
2. 流程繁杂,非标准化成“机器换人”阻碍
3C 产品零部件非常多,包括电池、充电器、耳机、屏幕、摄像头等;3C 产品生产流程繁杂,包括贴片、插件、焊接、检测、组装等几十道流程。复杂的流程构成了长产业链,导致 3C 产业链上的企业数量多且规模普遍较小。
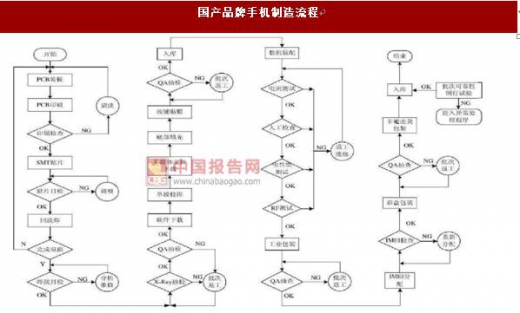
对大多机器人厂商而言,面对众多小客户的不同需求,需要针对性开发产品,每服务一个客户都需要大量时间和金钱来投入研发,这是导致国内机器人制造商和系统集成商规模大不起来的主要原因。客户需要的往往是非标产品,无法复制到其他环节。如果客户是世界知名的大厂,如富士康、伟创力等,考虑到需求量和知名度的提升,机器人厂商会愿意投入,但对于大量小客户而言,机器人厂商只有接不到大单时才会退而求其次。
对 3C 制造商而言,由于客户规模大多较小,可能一天要加工很多种产品,每种量都不大。以目前 3C 制造的柔性化程度,同一条生产线难以处理多种产品的制造,给 3C 制造“机器换人”带来阻碍。这也是为什么目前在 3C 制造过程中,机器人大部分被用于搬运、上下料和打磨等通用型的环节中。
对系统集成商而言,设备售后服务成本过高,导致其生存困难。由于目前 3C 机器人的应用还很不成熟,使用过程中问题频繁出现,3C 厂商的工程师很难学会维护机器人,因此后续维护费用大多由系统集成商自己承担。一个工程师月薪 15000 元,一家 3C 厂商客户就要绑住几个工程师,对系统集成商是一笔很大的费用,阻碍其业务扩展。
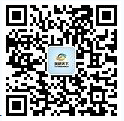
【版权提示】观研报告网倡导尊重与保护知识产权。未经许可,任何人不得复制、转载、或以其他方式使用本网站的内容。如发现本站文章存在版权问题,烦请提供版权疑问、身份证明、版权证明、联系方式等发邮件至kf@chinabaogao.com,我们将及时沟通与处理。