玻璃的成本结构?
燃料、纯碱是玻璃生产成本占比最大的两类成本,合计约占总成本的 60%以上。
玻璃目前有四种主要燃料:
一是重油,包括乙烯焦油、煤焦油等燃料油;
二是石油焦(中硫,1.5%-3%硫份),2009 年开始大量使用,是目前的主流燃料,主要用于中低端玻璃生产;
三是天然气,清洁能源,目前只有少数高端玻璃生产线采用;
四是煤制气,原料块煤会产生严重的粉尘污染,主要是沙河、东北与西北等地的中低端玻璃生产线使用。
不同企业不同生产线使用的燃料不一,甚至有混烧情况。通常一吨玻璃消耗重油或石油焦 0.16-0.18 吨、天然气 200 立方左右。
原材料中纯碱价格波动较大。玻璃原料主要包括纯碱、石英砂、芒硝、白云石、石灰石、长石、碳粉等,其中纯碱和石英砂占比最大,分别占到 54%和 27%。纯碱属于化工产业链,为外生成本,所以其价格变动对于玻璃生产成本影响较大。通常一吨玻璃消耗重质纯碱约为 0.2-0.22 吨,相当于每重箱玻璃消耗纯碱 0.01 吨。
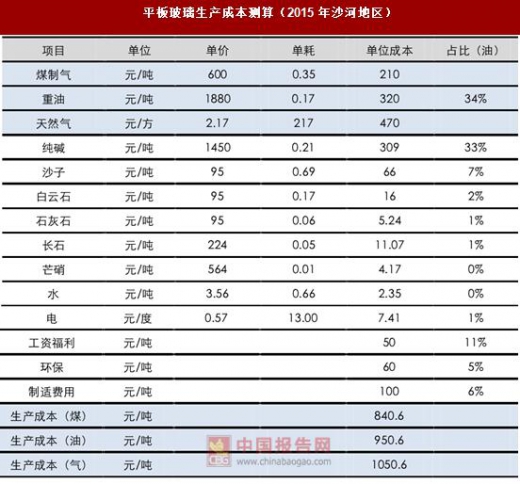
玻璃的环保问题?
从 2014 年 1 月 1 日起,《平板玻璃工业大气污染物排放标准》排放标准正式开始执行,玻璃熔窑排放上限为颗粒物 50mg/m3,二氧化硫 400mg/m3,氮氧化物 700mg/m3,部分省份地区甚至要求烟气中的氮氧化物排放要达到 350 mg/m3。
对玻璃窑炉烟气进行脱硝脱硫除尘一般采取以下技术:
1)脱硝工艺,主要包括选择性催化还原(SCR)、选择性非催化还原反应(SNCR)和联合脱硝技术,其中 SCR 是目前应用最广泛的技术,利用还原剂(如氨水或液氨)在一定的温度(280℃~400℃)和催化剂作用下,选择性地将烟气中的 NOx 还原为无害的 N2 和 H2O,脱硝效率可达 70%~95%。
2)脱硫工艺,当前比较成熟的玻璃窑炉脱硫技术有湿法脱硫(石灰石石膏法、双碱法、氧化镁法、氨法)半干法、高温干法。
3)除尘工艺,当前比较成熟的技术有电除尘、布袋除尘、超强湍流技术。
无论是新建还是复产生产线均须达到环保标准,通常一条浮法玻璃生产线脱硝脱硫治理投资需 1500 万元左右,对于一条日熔量为 600t 的生产线而言,相当于复产成本增加了3-4 元/重箱,对于小规模的生产线复产成本更高。除一次性设备投入外还有运营费用,每年环保成本约为 3 元/重箱。
虽然目前玻璃产线基本都安装环保设备,但环保设备持续运作的成本,以及环保趋严后燃料结构的改进,对新增和现有产能均存在制约。至于环保对下游加工企业的开工限制,由于仅影响阶段性出货,其影响有限且短暂。
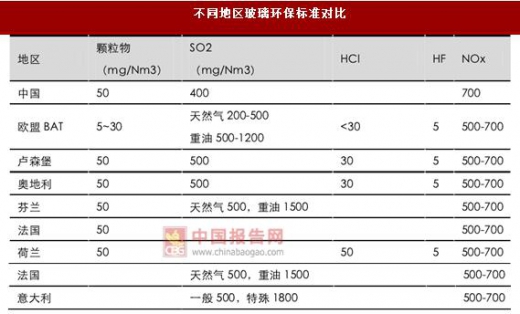
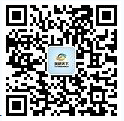
【版权提示】观研报告网倡导尊重与保护知识产权。未经许可,任何人不得复制、转载、或以其他方式使用本网站的内容。如发现本站文章存在版权问题,烦请提供版权疑问、身份证明、版权证明、联系方式等发邮件至kf@chinabaogao.com,我们将及时沟通与处理。