钢铁工业是我国工业领域主要排污大户之一。根据 2015 年环境统计年报,全国重点调查了 16.16 万家工业企业,其中钢铁冶炼加工企业 3476 家,排放二氧化硫、氮氧化物、烟粉尘分别为 173.6 万吨、104.3 万吨、357.2 万吨,占重点调查工业企业排放量的比例分别为12.4%、9.6%、32.2%。钢铁冶炼加工企业拥有废气治理设施 18572 套,其中,除尘设施 16337 套,脱硫设施 1174 套,脱硝设施数 63 套。
钢铁行业的大气污染主要来自于烧结环节,污染物主要是颗粒物、二氧化硫、氮氧化物。现行的排放标准是:一般地区排放限值为颗粒物 50mg/m3、二氧化硫 200mg/m3、氮氧化物 300mg/m3;特别排放限值为颗粒物 40mg/m3、二氧化硫 180mg/m3、氮氧化物 300mg/m3。
全国烧结设备都已安装除尘、脱硫设施,但是钢铁企业目前普遍未安装脱硝设备,氮氧化物具有较大减排潜力。因此,2017 年 6 月,环保部发布《钢铁烧结、球团工业大气污染物排放标准》等 20 项国家污染物排放标准修改单的公告征求意见稿,将钢铁烧结环节的标准提高为颗粒物 20mg/m3、二氧化硫 50mg/m3、氮氧化物 100mg/m3,提升幅度超出市场预期。
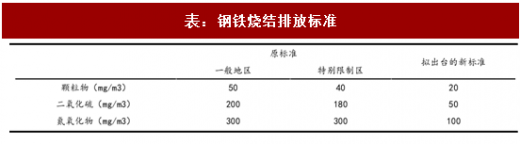
技术方面,我国烧结烟气脱硫技术已初步形成,目前已投运的脱硫工艺中,主流工艺包括石灰石-石膏法脱硫工艺、循环流化床、氨硫胺法等。从现有烧结脱硫技术投资状况来看,前期少数钢铁脱硫工程的投资基本都能控制在业主的承受范围内,但存在运行成本偏高的现象,分析认为主要是个别项目中标过程中打价格战,在实际施工过程中对吸收塔的尺寸与钢结构予以缩减,致使塔内烟气流速过大,系统负荷加剧,除雾器寿命缩短,烟气携带浆液由烟囱外排,造成“石膏雨”现象,由此带来高运行费和高排污费。新标准的执行将带来原有脱硫系统的改造需求。而钢铁行业烧结烟气脱硝工作还未全面启动,随着新标准的出台,未来脱硫脱硝协同一体化技术会是重要的发展方向。
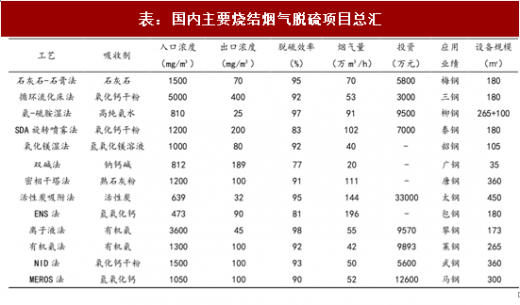
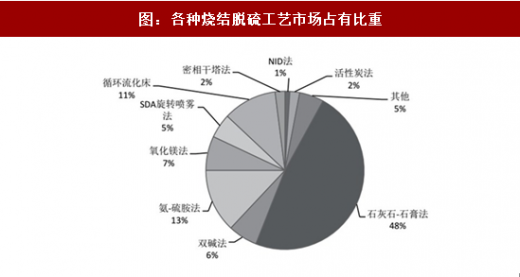
根据环保部测算:按照烧结机面积平均 180 平米为例,若采用电除尘+半干法脱硫除尘+中温 SCR 协同净化工艺,污染治理设施投资约 8200 万元,年运行维护费用约 2800 万元,生产吨烧结矿的环保成本为 11 元-15 元;若采用电除尘+活性炭协同治理工艺,污染治理设施投资约 1 亿元,年运行维护费用约 2600 万元,生产吨烧结矿的环保成本为 10 元~14 元。
我国现有烧结机 900 台左右,烧结机面积约 12 万平米,大部分烧结机都还没有装备脱硝设备,部分脱硫设备也达不到新的排放标准。每平米烧结机的脱硫设备投资约为 10-20 万元,脱硝设备投资预计在 20-30 万元。保守估计,新标准正式出台后预计将带动钢铁行业除尘脱硫脱硝设备订单 400-600 亿元,而这些订单预计将在未来 2 年集中释放。
二、工业锅炉煤改气
由于我国“富煤、贫油、少气”的资源特点,我国锅炉以燃煤为主,而燃煤工业锅炉保有量大、分布广、能耗高、污染重,能效和污染控制整体水平与国外相比有一定的差距,节能减排潜力巨大。
截止 2015 年,全国在用工业锅炉保有量约 57 万台,总蒸发量为 304 万吨/小时,其中燃煤工业锅炉约为 45.9 万台,占全国工业锅炉总台数的 80.5%左右,年耗煤量约 7 亿吨。
参考观研天下发布《2018-2023年中国环保行业市场现状深度调研与投资方向评估分析报告》
燃煤工业锅炉是城市大气污染的主要贡献源之一,也是仅次于燃煤发电的第二大煤烟型污染源,烟尘排放约占全国排放总量的 33%,二氧化硫排放量约占全国排放总量的 27%,氮氧化物排放量占全国排放总量的 9%。大范围、长时间严重的雾霾天气与燃煤工业锅炉区域高强度、低空排放的特点密切相关。
我国燃煤锅炉技术装备落后,大多数燃煤工业锅炉容量较小,单台平均容量仅为 3.8 吨/时,其中 2 吨/时以下台数占比达 66.5%,并且有部分老旧锅炉仍在使用。10 吨/时以下的燃煤工业锅炉大多没有配置有效的除尘装置,基本没有脱硫脱硝设施,排放超标严重。为解决燃煤锅炉污染问题,我国 2013 年起出台的多项环保与能源政策中都对燃煤锅炉提出改造要求。
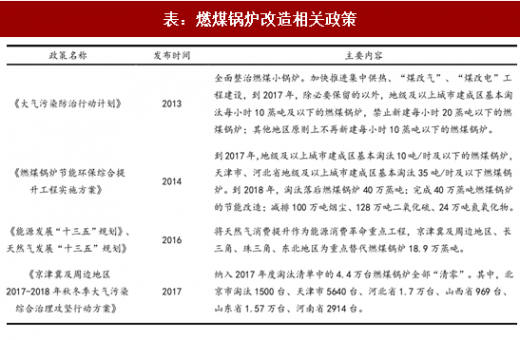
2013年国务院印发的《大气污染防治行动计划》中就明确“全面整治燃煤小锅炉。加快推进集中供热、“煤改气”、“煤改电”工程建设,到 2017 年,除必要保留的以外,地级及以上城市建成区基本淘汰每小时 10 蒸吨及以下的燃煤锅炉,禁止新建每小时 20 蒸吨以下的燃煤锅炉;其他地区原则上不再新建每小时 10 蒸吨以下的燃煤锅炉。在供热供气管网不能覆盖的地区,改用电、新能源或洁净煤,推广应用高效节能环保型锅炉。在化工、造纸、印染、制革、制药等产业集聚区,通过集中建设热电联产机组逐步淘汰分散燃煤锅炉。”
2014年发改委、环保部等 7 部委联合印发的《燃煤锅炉节能环保综合提升工程实施方案》中提出“到 2017 年,地级及以上城市建成区基本淘汰 10 吨/时及以下的燃煤锅炉,天津市、河北省地级及以上城市建成区基本淘汰 35 吨/时及以下燃煤锅炉。到 2018 年,淘汰落后燃煤锅炉 40 万蒸吨;完成 40 万蒸吨燃煤锅炉的节能改造;减排 100 万吨烟尘、128 万吨二氧化硫、24 万吨氮氧化物。”
2016 年国家发改委印发的《能源发展“十三五”规划》以及《天然气发展“十三五”规划》中将天然气消费提升作为能源消费革命重点工程,以京津冀、长三角、珠三角、东北地区为重点,推进重点城市“煤改气”工程,扩大城市高污染燃料禁燃区范围,大力推进天然气替代步伐,替代管网覆盖范围内的燃煤锅炉、工业窑炉、燃煤设施用煤和散煤。
天然气工业锅炉较燃煤锅炉污染物排放大幅降低,燃气锅炉二氧化硫排放量是煤炭锅炉的 17%;氮氧化物排放量是煤炭锅炉的 20%;此外,天然气锅炉没有粉尘排放。
按照国家发改委规划,京津冀及周边地区、长三角、珠三角、东北地区为重点替代燃煤锅炉 18.9 万蒸吨。从用气量增长来看,按照蒸汽锅炉一年运转 4000 小时,一吨蒸汽需要消耗 75-85 立方米天然气进行测算,替代燃煤锅炉 18.9 万蒸吨将增加天然气消费量 570-640 亿方。
从初始投资来看,按照每蒸吨改造投资 15-20 万元测算,改造 18.9 万蒸吨燃煤锅炉将带动投资 284 亿-378 亿元。
三、油田污泥处置
由于含油污泥处理技术相对落后,以及环保执法不严,我国油田污泥存在大量未经处理随意堆存的现象,对土壤、地下水造成严重污染。随着 2016 年“土十条”的出台,以及中央环保督察带来的环保风暴,油田污泥面临存量与增量污泥处置的巨大市场。
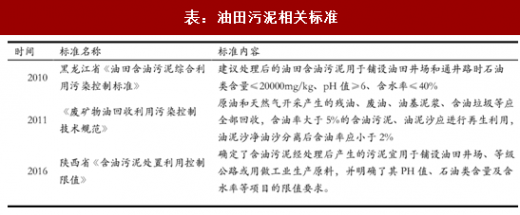
黑龙江省《油田含油污泥综合利建议处理后的油田含油污泥用于铺设油田井场和通井路时石油2010 用污染控制标准》 类含量≤20000mg/kg、pH 值≥6、含水率≤40%
原油和天然气开采产生的残油、废油、油基泥浆、含油垃圾等应《废矿物油回收利用污染控制2011 全部回收,含油率大于 5%的含油污泥、油泥沙应进行再生利用,技术规范》油泥沙净油沙分离后含油率应小于 2% 确定了含油污泥经处理后产生的污泥宜用于铺设油田井场、等级陕西省《含油污泥处置利用控制2016 公路或用做工业生产原料,并明确了其 PH 值、石油类含量及含限值》 水率等项目的限值要求。
根据产生的情况不同,油田污泥一般分为:①各类除油设备、立式沉降罐、储罐及回收水池等设施清理或排放的污泥,一般油含量10%~30%;②油水井测试、作业产生的落地油泥,油含量不确定; ③污油回收站产生的含油污泥,一般含油在 5%~20%;④基建施工、管道设备穿孔产生的落地油泥,油含量不确定。
油田污泥具有化学成分复杂、差异性大、处理难度大的特点,含油污泥一般由水包油、油包水以及悬浮固体杂质组成,是一种极其稳定的悬浮乳状液体系,含有大量的老化原油、蜡质、沥青质、胶体、固体悬浮物、细菌、盐类、酸性气体、腐蚀产物等,还包括生产过程中投加的大量絮凝剂、缓蚀剂、阻垢剂、杀菌剂等水处理剂。 由于含油污泥成分和物化性状受污水水质、处理工艺、加入药剂等诸多因素影响,因此给污泥处理带来了很大的难度。
常见处置技术主要有填埋、浓缩脱水、固化处理、化学出油、催化裂解或建材利用,由于起步较晚,技术普遍不够成熟。国外成熟工艺包括:焚烧、生物处理、溶剂萃取、热脱附等技术。
全国每年原油开采量约 2 亿吨,按照 1 当量原油产生 3%的污泥,则每年新产生油田污泥约 600 万吨。历史遗留污泥,假设仅考虑 2000 年以来的产量,2000 年以来我国原油产量约 32 亿吨,对应存量污泥约 1 亿吨。由于含油污泥属于危废,处置费用参照危废处理价格,取 3000 元/吨,则每年增量污泥空间为 200 亿元,存量污泥处置市场空间 3000 亿元,将在未来几年快速释放。
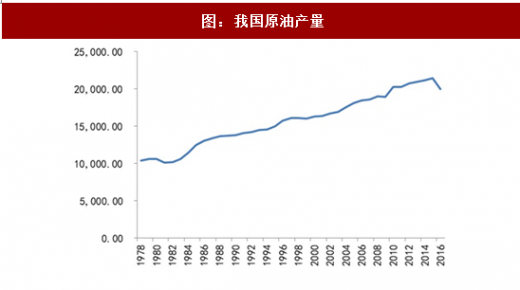
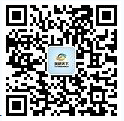
【版权提示】观研报告网倡导尊重与保护知识产权。未经许可,任何人不得复制、转载、或以其他方式使用本网站的内容。如发现本站文章存在版权问题,烦请提供版权疑问、身份证明、版权证明、联系方式等发邮件至kf@chinabaogao.com,我们将及时沟通与处理。