日本、台湾引领海外产能,中国占据产能龙头地位
2015年全世界电解铜箔年产量推估为42.7万吨,年增长率达5.4%。其中,中国大陆的电解铜箔产量在2015年年增长率达到10.5%,对整个全球电解铜箔2015年产量的增长是有力的拉动。由于近两三年,美国、日本铜箔企业的产能在大幅削减,且中国大陆产能在2015年与前一年基本持平,使得2015年全世界电解铜箔产能年增长率为-3.8%,年产能约达到59.6万吨。
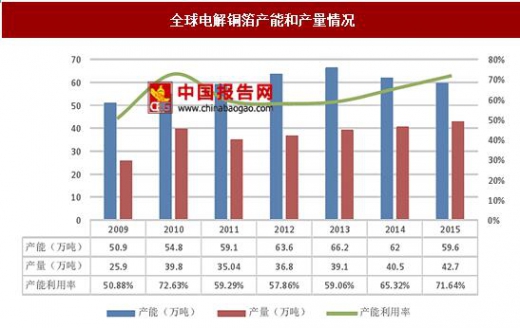
全球铜箔主要自亚洲,其中日本、台湾长期占据主导地位,尤其是在高精度电子铜箔领域技术优势明显。近几年国内铜箔产能发展迅速,同时日台两地的企业也纷纷在国内开设分厂,中国已成为新的产能供应龙头。目前国外铜箔厂主要有日本的古河电工,三井金属以及台湾的南亚等。
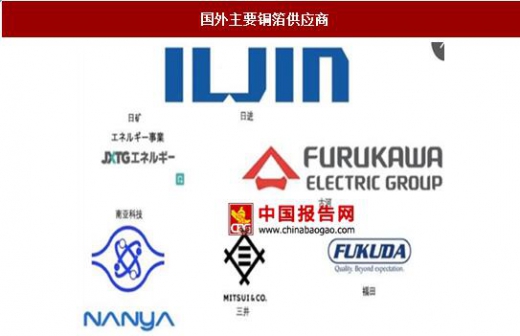
近两年国外标准铜箔产能逐步减少,同时海外铜箔的扩长周期长于国内,且市场处于供需平衡状态,进口铜箔对国内供给的冲击相对较小。
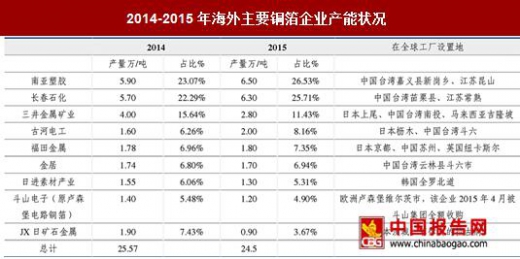
目前锂电铜箔产能主要集中在诺德股份、灵宝华鑫、嘉元科技、赣州逸豪及安徽铜冠(铜陵有色)这五家公司。截止2016年的数据显示,5家公司合计锂电铜箔产能约52400吨,占全国锂电铜箔总产能的84.33%,其中锂电铜箔龙头诺德股份的产能占比达到了39.19%,可以说目前锂电铜箔生产呈现寡头垄断格局,相对于电解液、隔膜,锂电铜箔的前五产能占比更高,一旦明确的供需缺口,锂电铜箔的涨价幅度和节奏将更为猛烈。
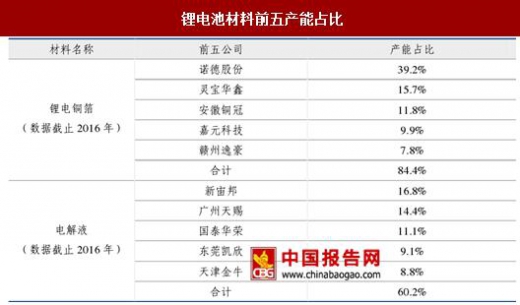
铜箔生产设备中最核心的是阴极辊,为电解铜箔生产核心,其品质决定了铜箔品质和良品率。阴极辊由纯钛制成,要求其表面晶粒细微几何形状一致,大小均匀,排列一致。阴极辊的生产技术壁垒极高,目前绝大多数的产能集中在日本企业,目前日本产品在国内的市占率达到了80%以上。同时由于阴极辊是非标准化产品,需要根据不同的铜箔生产线进行定制,所以阴极辊的生产周期较长,通常在一年左右。虽然目前国内阴极辊已逐步开始量产出货,但市场仍然对其质量和稳定性较为担忧。受制于核心设备的供给不足,铜箔扩产的难度依然较大。
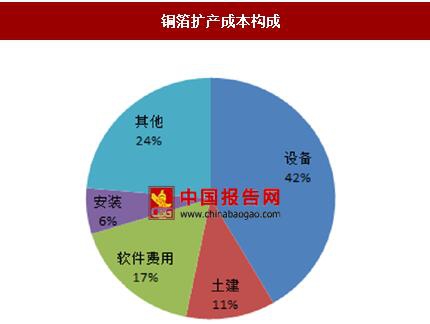
根据各厂商公布的扩产计划来看,2017年锂电铜箔可以释放的新增产能有限。行业前五大企业的新增产能主要集中在2018年释放,其他厂商新增产能主要集中于2017年开始试产,由于从试产到最终的产能释放仍需几个时间,同时考虑到下游电池厂商的认证时间,正在能够供应的锂电铜箔产能有限,我们预计2017年实际新增产能在2万吨左右。

同时,从标准铜箔生产线向锂电铜箔生产线也存在一定难度和成本问题。标准铜箔在生产环节上比锂电铜箔多一个尾端表面处理供需,同时两者在溶解液工序中的配方也有所不同。转产后,还面临下游电池厂商的验证问题,所以通常转产周期都在半年左右。
6μm及微孔铜箔引领未来发展趋势高端产品或成竞争核心
随着锂电池能量密度的不断提升,对锂电铜箔的要求也日趋严格,主要体现在对强度、表面粗糙度、延展性及厚度等方面的指标要求。尤其在铜箔厚度方面,较低的厚度可降低电池重量,增加其能量密度,目前呈现从9μm向8μm、再从8μm向6μm过度的趋势。厚度越薄,工艺难度越高,同时加工费越高。目前8μm加工费月4.5万/吨,而6μm的加工费高达8万/吨,在6μm领域只有诺德等少数几家公司可以生产,同时超薄铜箔在运输过程中易出现折皱、撕裂等情况,对整个环境指标要求极高。
另外,微孔铜箔日益成为市场关注重点,相较于传统铜箔,微孔更利于锂离子在电池中的扩散,能获得更好的浸透率和柔韧度,更适应未来动力锂电池的发展方向,目前各家正在抓紧技术储备,未来市场空间巨大。
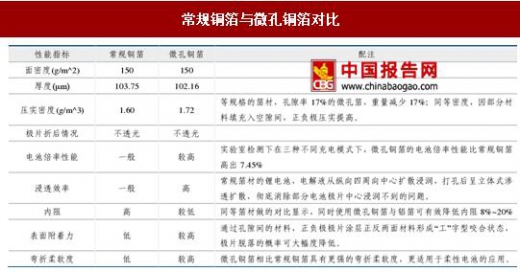
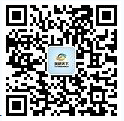
【版权提示】观研报告网倡导尊重与保护知识产权。未经许可,任何人不得复制、转载、或以其他方式使用本网站的内容。如发现本站文章存在版权问题,烦请提供版权疑问、身份证明、版权证明、联系方式等发邮件至kf@chinabaogao.com,我们将及时沟通与处理。